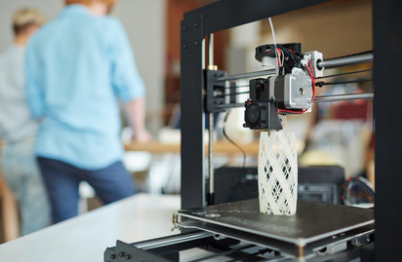
Kaizen integration into manufacturing processes can be difficult. The process is slow, requires time to procure inventory and ensure that all hands are on deck. It depends on the problem area, level of participation and the size of the firm that is involved in this process. You must follow the right implementation procedures and acquire the required resources to ensure the success of your manufacturing process improvement program. To make this strategy work, create a culture within your company that promotes continuous improvement.
Creating a company culture with a focus on improvement
Gallup polls found that 32% of Americans are not engaged in their work. 17.2% of these employees were actively disengaged. Kaizen culture encourages employee engagement which in turn will improve processes, reduce turnover and promote innovation. Engaged workers are more likely to innovate and contribute ideas, which will lead to higher productivity, customer satisfaction, and better customer service. Kaizen culture has many benefits beyond reducing waste and increasing productivity.
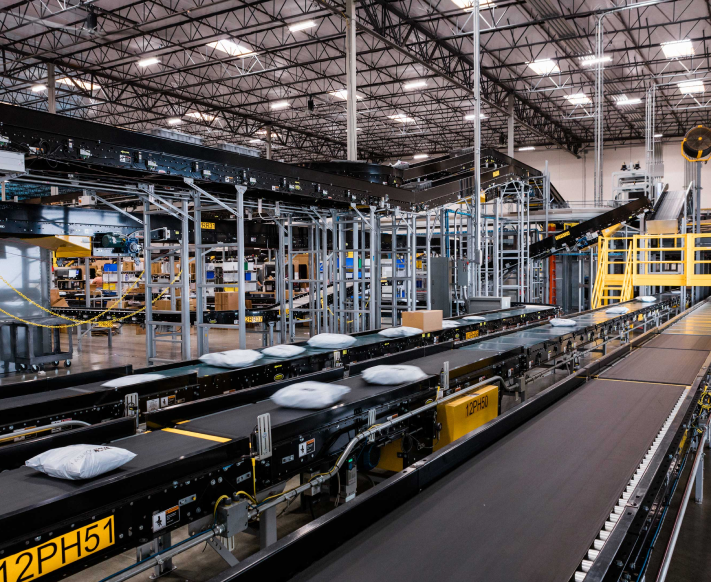
Kaizen is a philosophy that encourages continuous improvement in every area of a business. Rather than making big, sweeping changes that have little to no benefit, Kaizen is a method of incremental improvement. Kaizen can help reduce costs, increase productivity, improve quality, and improve customer satisfaction when implemented properly. It is also a great way to increase employee morale.
There are many obstacles to implementing Kaizen in manufacturing
Although there are many benefits to implementing kaizen, there are also some drawbacks. First, implementing Kaizen requires substantial changes to a company's management systems. It is possible to make the changes again after they have been implemented. Second, many businesses find it difficult to change existing work practices, which may pose a barrier to the implementation of kaizen.
Another common problem is that many manufacturing companies operate on a cycle of "feast and famine". When demand drops for their products and they don't have enough people to hire them, the machine shop will be in trouble. In such a scenario, they will have to layoff employees and close their doors. Implementing kaizen (continuous improvement) will keep these machine shops from falling into the "feast or feast" cycle. Kaizen is a way to increase efficiency in a shop and produce more products.
High success rate in kaizen implementation during manufacturing
Statistics show that Kaizen implementation in manufacturing is not a success. Only 10% percent of manufacturing companies have reported positive Kaizen outcomes. The implementation process does not have to be boring. Implementing Kaizen is an integral part of lean manufacturing. Here are some tips that will help you increase the success of your manufacturing business.
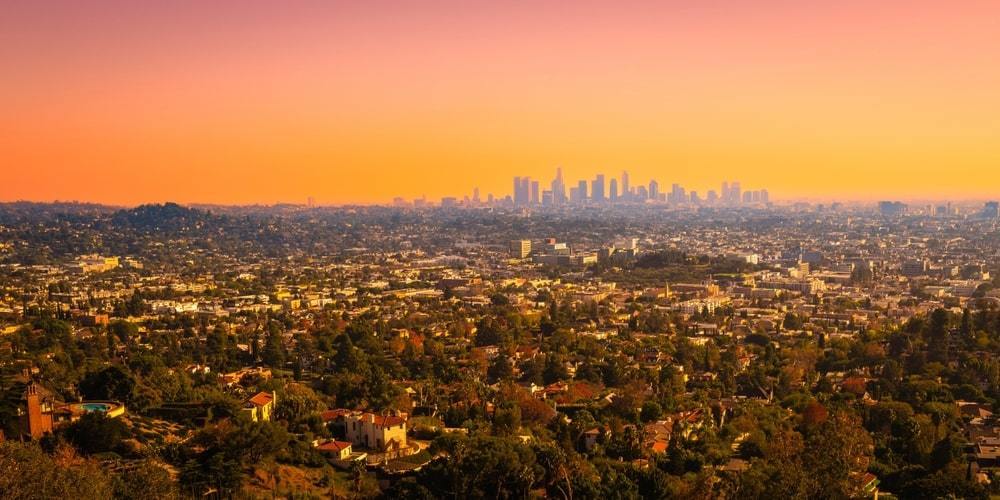
To begin kaizen, it is important to first understand current state processes. During the first step, data is collected and analyzed to identify the highest priorities. The next step is to test and verify improvements by performing a comparison of the before-and-after. Benefit-to-cost analysis can also be used to understand the impact of a specific improvement or the whole kaizen process. It is essential to track the results of kaizen cycles for 60-90 days to gauge the effectiveness of the program.
FAQ
How can manufacturing efficiency be improved?
The first step is to determine the key factors that impact production time. Then we need to find ways to improve these factors. If you don't know where to start, then think about which factor(s) have the biggest impact on production time. Once you've identified them all, find solutions to each one.
What is the difference between Production Planning and Scheduling?
Production Planning (PP), or production planning, is the process by which you determine what products are needed at any given time. Forecasting and identifying production capacity are two key elements to this process.
Scheduling refers the process by which tasks are assigned dates so that they can all be completed within the given timeframe.
What are the goods of logistics?
Logistics refers to all activities that involve moving goods from A to B.
These include all aspects related to transport such as packaging, loading and transporting, storing, transporting, unloading and warehousing inventory management, customer service. Distribution, returns, recycling are some of the options.
Logisticians make sure that the right product arrives at the right place at the correct time and in safe conditions. They help companies manage their supply chain efficiency by providing information on demand forecasts, stock levels, production schedules, and availability of raw materials.
They monitor shipments in transit, ensure quality standards, manage inventories, replenish orders, coordinate with suppliers and other vendors, and offer support services for sales, marketing, and customer service.
What are the four types in manufacturing?
Manufacturing is the process that transforms raw materials into useful products. It includes many different activities like designing, building and testing, packaging, shipping and selling, as well as servicing.
Statistics
- [54][55] These are the top 50 countries by the total value of manufacturing output in US dollars for its noted year according to World Bank.[56] (en.wikipedia.org)
- You can multiply the result by 100 to get the total percent of monthly overhead. (investopedia.com)
- Job #1 is delivering the ordered product according to specifications: color, size, brand, and quantity. (netsuite.com)
- (2:04) MTO is a production technique wherein products are customized according to customer specifications, and production only starts after an order is received. (oracle.com)
- According to the United Nations Industrial Development Organization (UNIDO), China is the top manufacturer worldwide by 2019 output, producing 28.7% of the total global manufacturing output, followed by the United States, Japan, Germany, and India.[52][53] (en.wikipedia.org)
External Links
How To
How to Use 5S to Increase Productivity in Manufacturing
5S stands in for "Sort", the "Set In Order", "Standardize", or "Separate". Toyota Motor Corporation was the first to develop the 5S approach in 1954. It assists companies in improving their work environments and achieving higher efficiency.
This method has the basic goal of standardizing production processes to make them repeatable. This means that daily tasks such as cleaning and sorting, storage, packing, labeling, and packaging are possible. Workers can be more productive by knowing what to expect.
Implementing 5S involves five steps: Sort, Set in Order, Standardize Separate, Store, and Each step requires a different action to increase efficiency. You can make it easy for people to find things later by sorting them. You arrange items by placing them in an order. You then organize your inventory in groups. Finally, when you label your containers, you ensure everything is labeled correctly.
This process requires employees to think critically about how they do their job. Employees need to understand the reasons they do certain jobs and determine if there is a better way. To be successful in the 5S system, employees will need to acquire new skills and techniques.
The 5S Method not only improves efficiency, but it also helps employees to be more productive and happier. Once they start to notice improvements, they are motivated to keep working towards their goal of increasing efficiency.