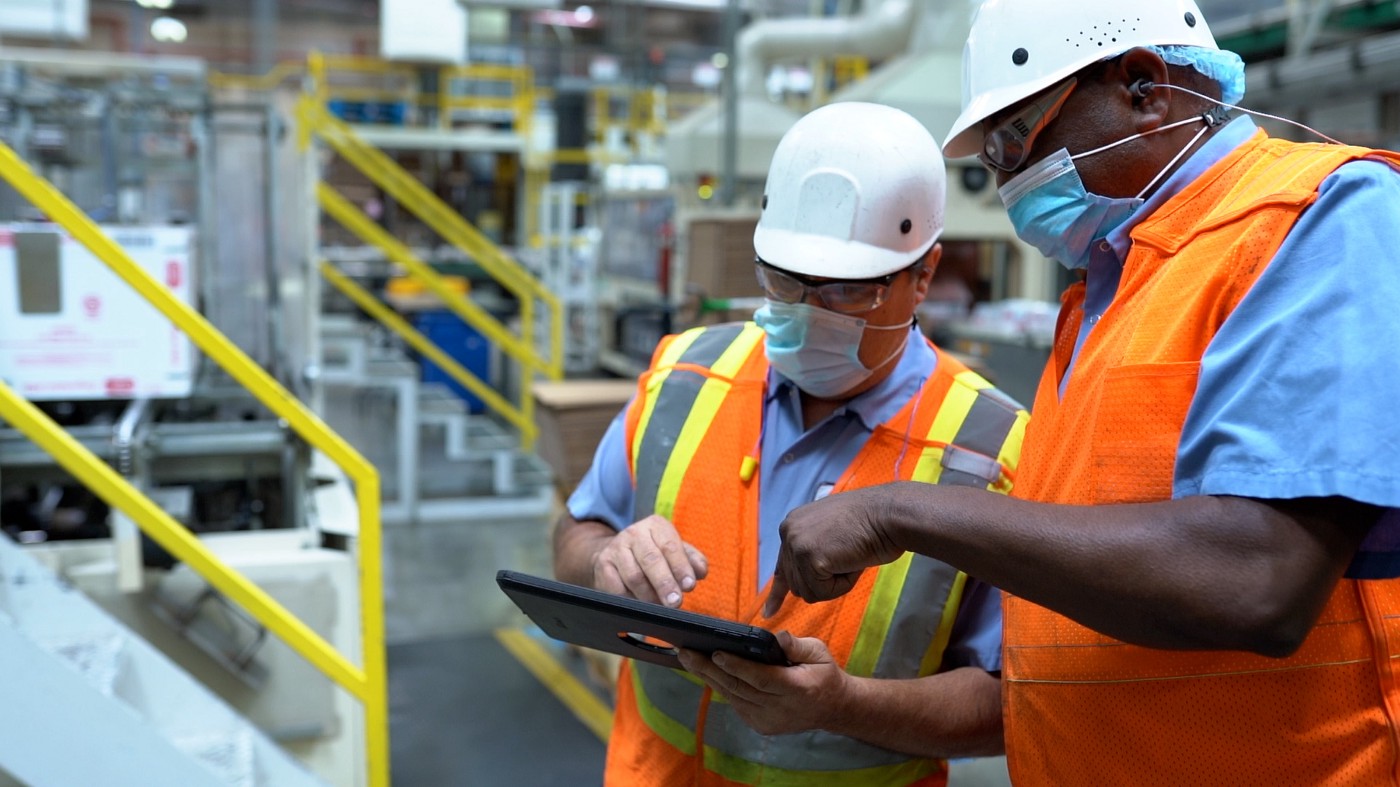
The United States ranks third among the largest manufacturers in the world. In Q1 2018, its manufacturing output topped $2.00 trillion. This is nearly twice what it was prior to the Great Recession. Despite a strong domestic economy and a robust manufacturing sector, the United States is still taking a cautious approach to its current problems. This is either due to a lack in investment or a shortage of skilled labor. We must be more aggressive in confronting the challenges that face our industry.
Jobs have declined by 5 million since 2000
Since 2000, the US has lost five millions manufacturing jobs. Some claim that the rise of trade with China is to blame. However, only about a quarter the decline in manufacturing jobs can be attributed to this. Not only was there trade with China, but manufacturing jobs were also lost on local markets that weren't competitive with Chinese imports. But there are many factors that contributed to the decline of manufacturing jobs. The following are some of the reasons:
During the last two decades, the US manufacturing sector lost nearly a third of its jobs. It was 17,000,000 in 1965. By 2010, it had fallen to 12,000,000. While the decline in manufacturing jobs is not the fault of trade, it has been the result of structural problems - a decline in capital investment, output, productivity, and trade deficits - which are not sustainable. Although productivity gains had a large role in the decline in manufacturing jobs, they weren't enough. Not productivity gains, but automation is the problem.
Strong demand for manufactured goods
The United States still has strong demand for manufactured goods despite a decline in consumer spending over the past decade. In 1945, personal expenditures on durable goods accounted for 58% of total spending, compared to just 28% today. The reason is that the price of making and selling these goods has fallen while their content has increased. As a result, the cost of computers, televisions, and sound equipment has fallen significantly.
The US has experienced a rebound in manufacturing activity which has helped boost the production of manufactured products. According to the Fifth District Manufacturing Activity Survey (Fifth District Manufacturing Activity Survey), demand is strong for manufactured goods, and production is on the rise. However supply chain bottlenecks are hindering output. Increased production has put pressure on supply chains. Many respondents reported experiencing supply chain disruptions that have affected their ability to keep necessary inventories. Backlogs have increased as well, and vendors lead times have been longer.
Over the past decade, the trade deficit for manufactured goods has more then doubled
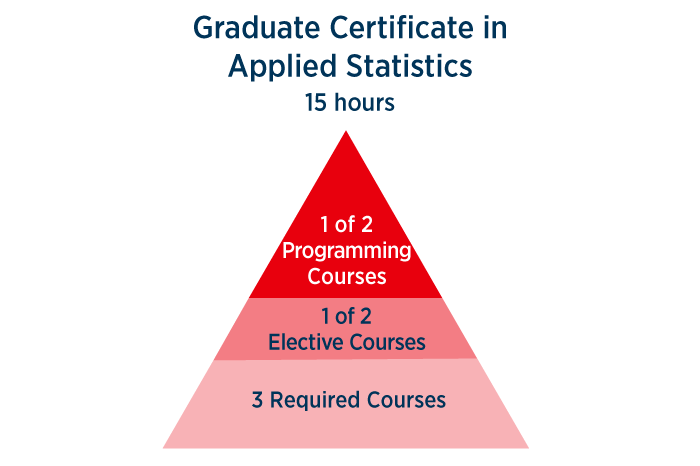
Economists worry that the U.S. will have a lower level of global growth and cause more instability among its trading counterparts. Some argue that the high imports of manufactured goods from the United States are not necessarily bad for its economy. This is essential to maintaining global economic stability. In fact, the trade deficit could be considered a necessary evil as the U.S. depends heavily on foreign markets to produce its economic output. High levels of foreign consumption may make it harder to achieve full-employment.
Since 2000, nearly two-thirds of the U.S. manufacturing goods trade deficit has increased. The increase in Chinese imports is partially responsible for the growing US deficit. But the larger problem is that this imbalance is concentrated in the manufacturing sector, where wages and employment have decreased since the 1990s. US manufacturing employment fell dramatically from 26% in 1970 to 8.5% in 2016. Some economists attribute this decline to China's increased competitiveness, but many others attribute it to automation, productivity improvements, and the shift in consumer demand away from goods to more services.
Industry has a shotgun approach
The US has a variety of advanced manufacturing initiatives. It is also well-established in this area. But some countries are attempting to introduce the internet of things to manufacturing. The US, on the other hand, focuses on diverse technologies and combines Internet advertising with traditional mass media. This results in a shotgun approach where companies concentrate on different technologies and seek a wide customer base.
FAQ
How does a production planner differ from a project manager?
The main difference between a production planner and a project manager is that a project manager is usually the person who plans and organizes the entire project, whereas a production planner is mainly involved in the planning stage of the project.
What are the differences between these four types?
Manufacturing is the process by which raw materials are transformed into useful products through machines and processes. Manufacturing involves many activities, including designing, building, testing and packaging, shipping, selling, service, and so on.
Are there any Manufacturing Processes that we should know before we can learn about Logistics?
No. You don't have to know about manufacturing processes before learning about logistics. Knowing about manufacturing processes will help you understand how logistics works.
Statistics
- According to the United Nations Industrial Development Organization (UNIDO), China is the top manufacturer worldwide by 2019 output, producing 28.7% of the total global manufacturing output, followed by the United States, Japan, Germany, and India.[52][53] (en.wikipedia.org)
- In 2021, an estimated 12.1 million Americans work in the manufacturing sector.6 (investopedia.com)
- It's estimated that 10.8% of the U.S. GDP in 2020 was contributed to manufacturing. (investopedia.com)
- [54][55] These are the top 50 countries by the total value of manufacturing output in US dollars for its noted year according to World Bank.[56] (en.wikipedia.org)
- According to a Statista study, U.S. businesses spent $1.63 trillion on logistics in 2019, moving goods from origin to end user through various supply chain network segments. (netsuite.com)
External Links
How To
How to Use lean manufacturing in the Production of Goods
Lean manufacturing refers to a method of managing that seeks to improve efficiency and decrease waste. It was created in Japan by Taiichi Ohno during the 1970s and 80s. He received the Toyota Production System award (TPS), from Kanji Toyoda, founder of TPS. The first book published on lean manufacturing was titled "The Machine That Changed the World" written by Michael L. Watkins and published in 1990.
Lean manufacturing is often defined as a set of principles used to improve the quality, speed, and cost of products and services. It emphasizes reducing defects and eliminating waste throughout the value chain. Just-in-time (JIT), zero defect (TPM), and 5S are all examples of lean manufacturing. Lean manufacturing emphasizes reducing non-value-added activities like inspection, rework and waiting.
Lean manufacturing can help companies improve their product quality and reduce costs. Additionally, it helps them achieve their goals more quickly and reduces employee turnover. Lean manufacturing is considered one of the most effective ways to manage the entire value chain, including suppliers, customers, distributors, retailers, and employees. Many industries worldwide use lean manufacturing. Toyota's philosophy is the foundation of its success in automotives, electronics and appliances, healthcare, chemical engineers, aerospace, paper and food, among other industries.
Five fundamental principles underlie lean manufacturing.
-
Define Value: Identify the social value of your business and what sets you apart.
-
Reduce Waste - Eliminate any activity that doesn't add value along the supply chain.
-
Create Flow - Make sure work runs smoothly without interruptions.
-
Standardize and Simplify – Make processes as consistent, repeatable, and as simple as possible.
-
Build relationships - Develop and maintain personal relationships with both your internal and external stakeholders.
Lean manufacturing is not a new concept, but it has been gaining popularity over the last few years due to a renewed interest in the economy following the global financial crisis of 2008. Many businesses have adopted lean production techniques to make them more competitive. Some economists even believe that lean manufacturing can be a key factor in economic recovery.
Lean manufacturing has many benefits in the automotive sector. These include improved customer satisfaction, reduced inventory levels, lower operating costs, increased productivity, and better overall safety.
You can apply Lean Manufacturing to virtually any aspect of your organization. It is especially useful for the production aspect of an organization, as it ensures that every step in the value chain is efficient and effective.
There are three main types:
-
Just-in Time Manufacturing: This lean manufacturing method is commonly called "pull systems." JIT stands for a system where components are assembled on the spot rather than being made in advance. This strategy aims to decrease lead times, increase availability of parts and reduce inventory.
-
Zero Defects Manufacturing (ZDM),: ZDM is a system that ensures no defective units are left the manufacturing facility. It is better to repair a part than have it removed from the production line if it needs to be fixed. This is true even for finished products that only require minor repairs prior to shipping.
-
Continuous Improvement (CI),: Continuous improvement aims improve the efficiency and effectiveness of operations by continuously identifying issues and making changes to reduce waste. Continuous improvement involves continuous improvement of processes and people as well as tools.