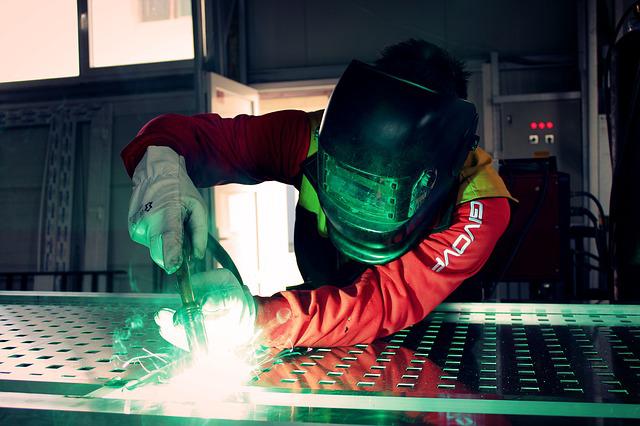
To transform your manufacturing process into an efficient machine, you must understand the five S's of Lean Manufacturing. They are Standardize. Straighten. Shine. and Sustain. Here are some steps you should follow. You need to train your frontline personnel and team leaders in order to make the most of your lean transformation.
Standardize
Clean up and organize your workspace as the first step in the 5S Process. Although this can seem like a single-time task, it can be made into a routine by standardizing the process. To create a consistent approach for 5S tasks you can use visual cues and checklist templates.
These five s’s of lean can help improve the productivity and efficiency of your workplace. This will encourage staff to be organised and make their work easier. A clean and well-organized work environment will improve efficiency. You can improve safety in your workplace by using the five s’s of lean. A well-organized workplace will reduce accidents and mistakes, increase productivity, and help you avoid them.
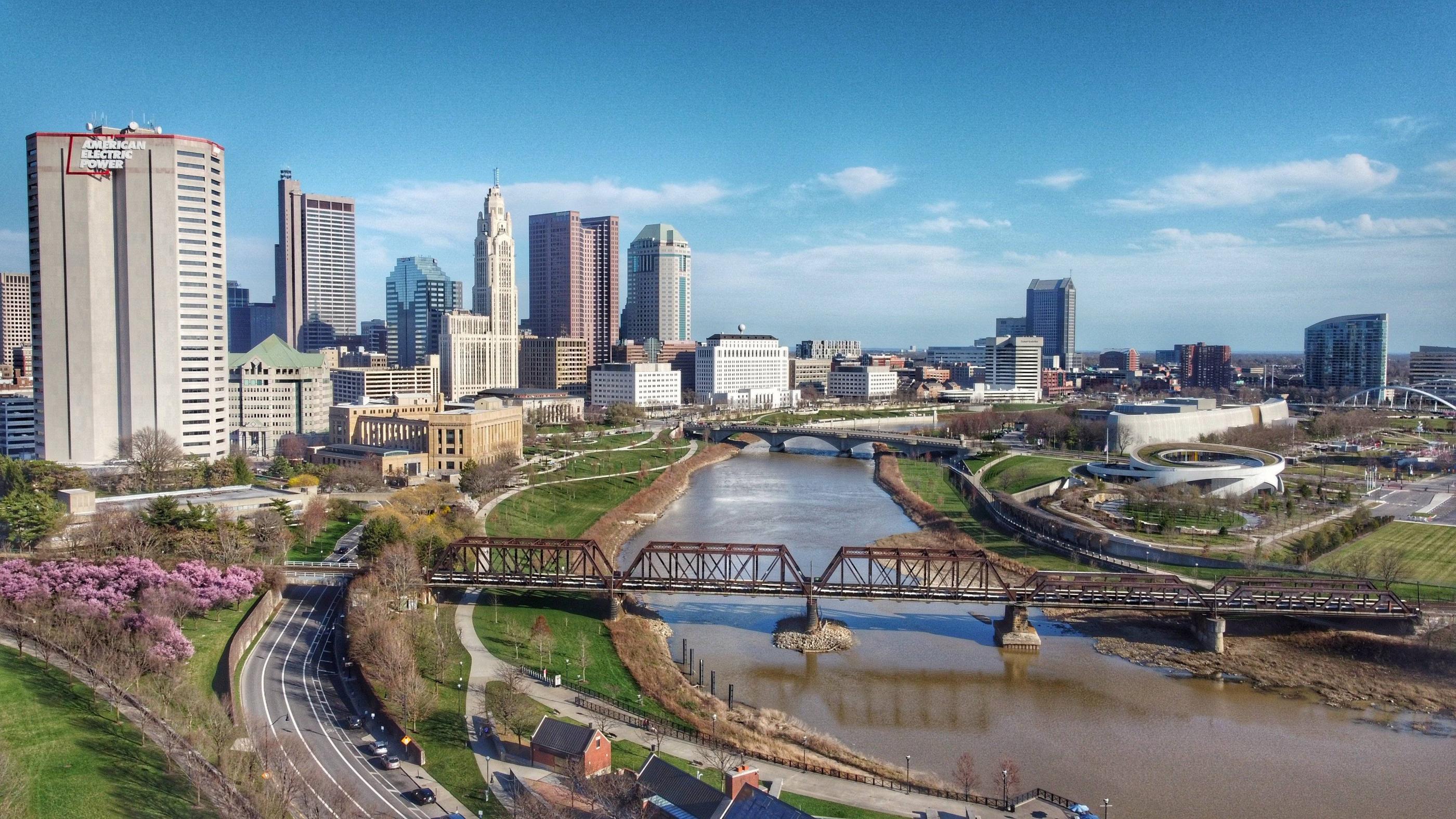
Straighten
Not having to do it all is necessary to achieve your 5 S's of Lean. Practicing lean principles in a systematic manner helps companies to improve their business processes. By organizing components in an assembly line, workers can find what they are looking for more quickly. This will help reduce the time spent looking for lost parts and improve safety in the workplace.
This will allow you to reduce the number items in each area. It will also help you save money on consumables. This allows you to significantly reduce your office supplies bill. Straightening work cells not only helps you save money but it also increases the efficiency of your production process by improving quality, safety, and standard work.
Shine
Shine is a step that inspects the workspace and points out potential problems. Shine inspects tools and equipment to help improve flow and reduce waste. Shine makes it easier to maintain a workspace. Shine also aids in standardizing the layout of work areas to increase productivity.
Shine is one tool used in lean manufacturing. This technique streamlines and automates work processes to reduce waste and increase efficiency. It can be applied to any industry, including manufacturing. In this way, it applies the 5S principles across a business. It reduces inventory, work in progress, and supplies stock.
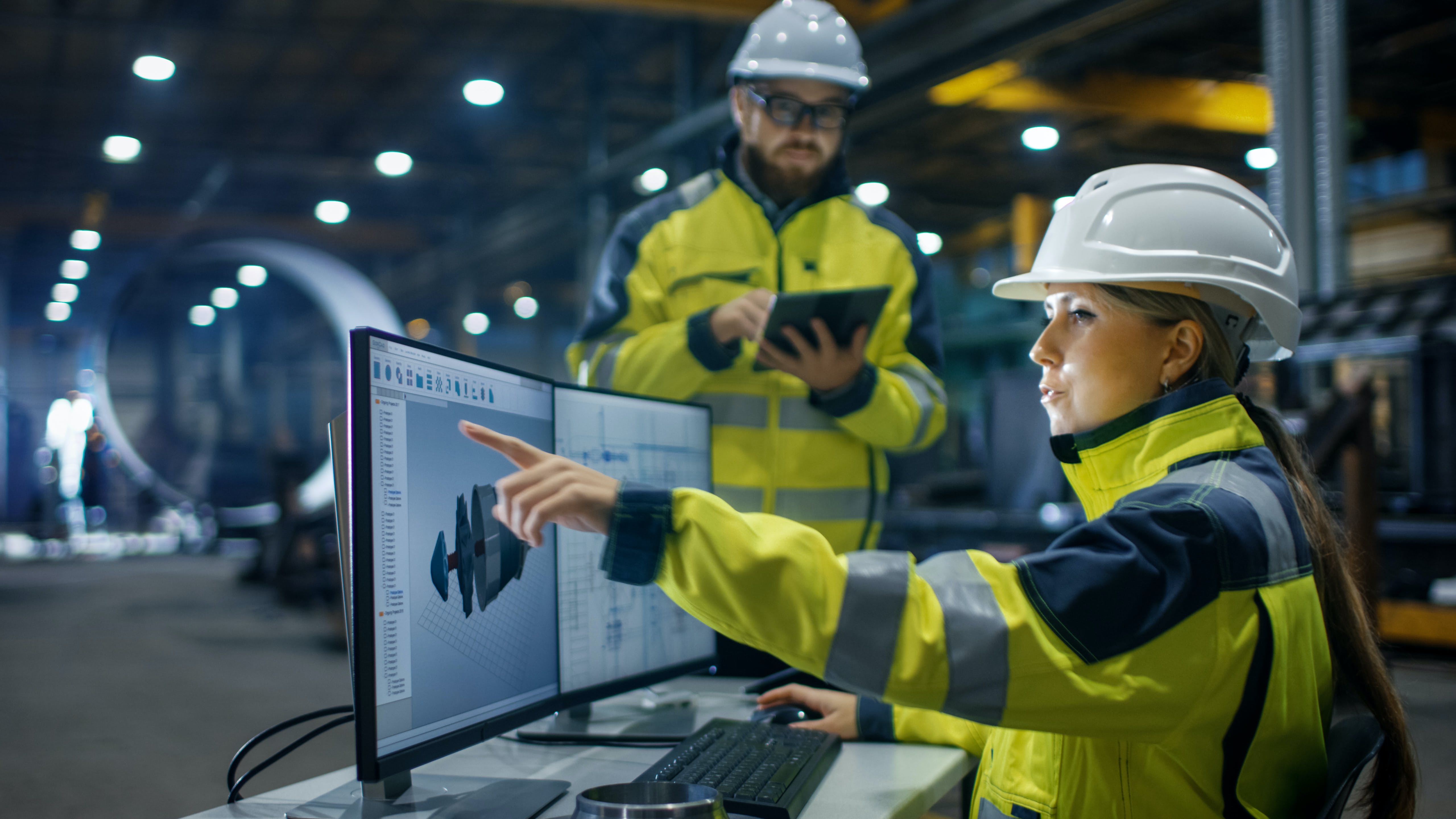
Maintain
In order to sustain the 5 s’s of lean, you need to bring back a standardized system into a facility. This is a process that is meant to be continuous and should be repeated often to ensure the facility works at its best. To do this, employees should be trained to perform 5S audits themselves.
The 5S approach focuses on reducing waste and optimizing productivity while maintaining a clean and orderly workplace. The 5S approach to organizing workplaces applies the five principles in the Toyota Production System. Hiroyuki Hirano created it post-war Japan to improve manufacturing efficiency.
FAQ
What is production planning?
Production planning is the process of creating a plan that covers all aspects of production. This includes scheduling, budgeting and crew, location, equipment, props, and more. This document aims to ensure that everything is planned and ready when you are ready to shoot. This document should include information about how to achieve the best results on-set. This includes location information, crew details, equipment specifications, and casting lists.
First, you need to plan what you want to film. You may have already chosen the location you want, or there are locations or sets you prefer. Once you have identified your locations and scenes, you can start working out which elements you require for each scene. For example, you might decide that you need a car but don't know exactly what model you want. To narrow your options, you can search online for available models.
After you have chosen the right car, you will be able to begin thinking about accessories. Do you need people sitting in the front seats? Or maybe you just need someone to push the car around. Perhaps you would like to change the interior colour from black to white. These questions will help you determine the exact look and feel of your car. You can also think about the type of shots you want to get. Do you want to film close-ups, or wider angles? Maybe you want the engine or the steering wheels to be shown. All of these things will help you identify the exact style of car you want to film.
Once you've determined the above, it is time to start creating a calendar. You will know when you should start and when you should finish shooting. A schedule for each day will detail when you should arrive at the location and when you need leave. It will help everyone know exactly what they have to do and when. If you need to hire extra staff, you can make sure you book them in advance. It is not worth hiring someone who won’t show up because you didn’t tell him.
Your schedule will also have to be adjusted to reflect the number of days required to film. Some projects only take one or two days, while others may last weeks. When creating your schedule, be aware of whether you need more shots per day. Multiple takes at the same place will result in higher costs and longer completion times. If you are unsure if you need multiple takes, it is better to err on the side of caution and shoot fewer takes rather than risk wasting money.
Budgeting is another crucial aspect of production plan. You will be able to manage your resources if you have a realistic budget. It is possible to reduce the budget at any time if you experience unexpected problems. You shouldn't underestimate the amount you'll spend. You'll end up with less money after paying for other things if the cost is underestimated.
Production planning can be a complex process. However, once you know how everything works together it will become easier to plan future projects.
What are the responsibilities for a manufacturing manager
The manufacturing manager should ensure that every manufacturing process is efficient and effective. They should also be aware of any problems within the company and act accordingly.
They should also be able communicate with other departments, such as sales or marketing.
They should be up to date on the latest trends and be able apply this knowledge to increase productivity and efficiency.
How does a Production Planner differ from a Project Manager?
The difference between a product planner and project manager is that a planer is typically the one who organizes and plans the entire project. A production planner, however, is mostly involved in the planning stages.
What is the difference between Production Planning, Scheduling and Production Planning?
Production Planning (PP), also known as forecasting and identifying production capacities, is the process that determines what product needs to be produced at any particular time. This can be done by forecasting demand and identifying production capabilities.
Scheduling is the process that assigns dates to tasks so they can get completed within a given timeframe.
What are manufacturing and logistic?
Manufacturing is the production of goods using raw materials. Logistics manages all aspects of the supply chain, including procurement, production planning and distribution, inventory control, transportation, customer service, and transport. Manufacturing and logistics are often considered together as a broader term that encompasses both the process of creating products and delivering them to customers.
What do you mean by warehouse?
A warehouse is an area where goods are stored before being sold. It can be an outdoor or indoor area. In some cases it could be both indoors and outdoors.
What is meant by manufacturing industries?
Manufacturing Industries are companies that manufacture products. The people who buy these products are called consumers. These companies use various processes such as production, distribution, retailing, management, etc., to fulfill this purpose. They manufacture goods from raw materials using machines and other equipment. This covers all types of manufactured goods including clothing, food, building supplies and furniture, as well as electronics, tools, machinery, vehicles and pharmaceuticals.
Statistics
- Many factories witnessed a 30% increase in output due to the shift to electric motors. (en.wikipedia.org)
- (2:04) MTO is a production technique wherein products are customized according to customer specifications, and production only starts after an order is received. (oracle.com)
- In 2021, an estimated 12.1 million Americans work in the manufacturing sector.6 (investopedia.com)
- [54][55] These are the top 50 countries by the total value of manufacturing output in US dollars for its noted year according to World Bank.[56] (en.wikipedia.org)
- In the United States, for example, manufacturing makes up 15% of the economic output. (twi-global.com)
External Links
How To
How to Use Six Sigma in Manufacturing
Six Sigma can be described as "the use of statistical process control (SPC), techniques to achieve continuous improvement." Motorola's Quality Improvement Department, Tokyo, Japan, developed it in 1986. Six Sigma's basic concept is to improve quality and eliminate defects through standardization. Many companies have adopted this method in recent years. They believe there is no such thing a perfect product or service. Six Sigma's main objective is to reduce variations from the production average. This means that you can take a sample from your product and then compare its performance to the average to find out how often the process differs from the norm. If the deviation is excessive, it's likely that something needs to be fixed.
Understanding the nature of variability in your business is the first step to Six Sigma. Once you've understood that, you'll want to identify sources of variation. Also, you will need to identify the sources of variation. Random variations are caused by human errors. Systematic variations can be caused by outside factors. These are, for instance, random variations that occur when widgets are made and some fall off the production line. However, if you notice that every time you assemble a widget, it always falls apart at exactly the same place, then that would be a systematic problem.
Once you identify the problem areas, it is time to create solutions. It might mean changing the way you do business or redesigning it entirely. Once you have implemented the changes, it is important to test them again to ensure they work. If they fail, you can go back to the drawing board to come up with a different plan.