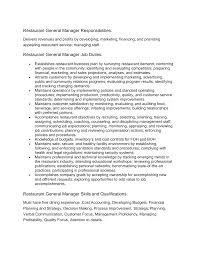
Heijunka was created originally by Toyota, a Japanese car manufacturer. It helps reduce waste in production by making sure the production schedule meets customer demand. The production schedule is consistent with customer demand, which reduces waste. Heijunka helps manufacturers to meet customer demands and improve their profits.
Heijunka can be described as a method of coordinating small production batches across different manufacturing lines. It's used to improve efficiency when multi-step production is being done, particularly when just-in time principles are used. It is also a part of the Toyota Production System. It helps reduce waste by leveling production, mixing products and minimizing batch sizes.
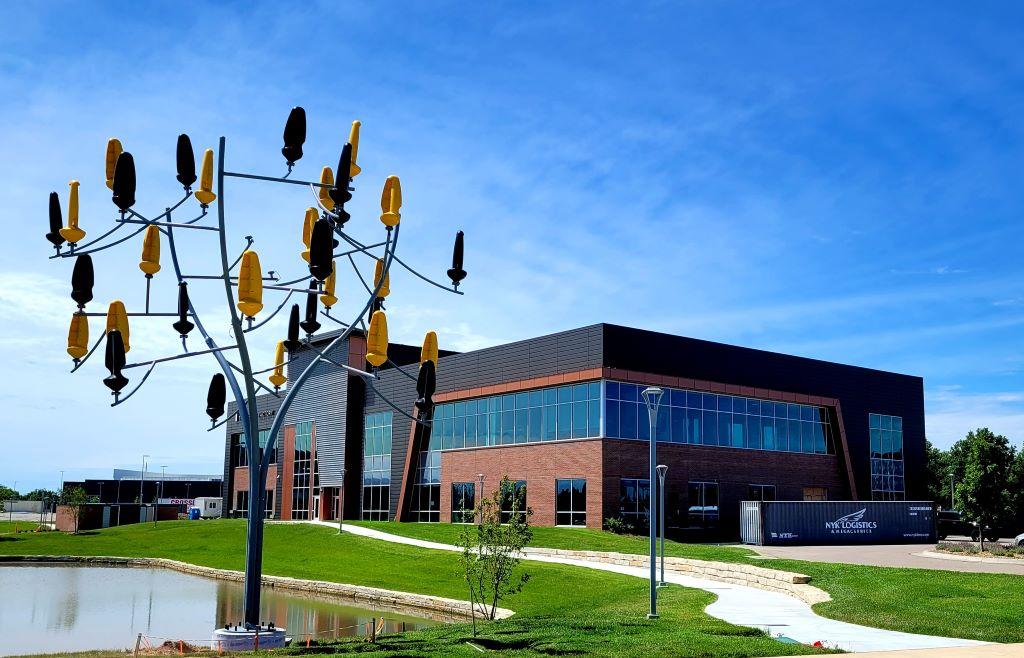
There are two possible ways to use heijunka. One method is the use of a Heijunka Box, which is a grid consisting of small boxes fixed to or mounted on a surface. It allows production personnel visualize the production process and schedules them. Magnetic cards are another way to implement the heijunka.
Toyota dealers use Heijunka, a production technique to ensure quick changeovers. It is also part of Toyota's Lean manufacturing framework. Heijunka can be used to improve production and inventory management. Heijunka helps to make better use of both labor and equipment. It provides a lean production system that reduces waste, thereby making better products available to customers.
The takt rate, also called the customer buying price, is essential in order to use heijunka. This is the time it takes for a product to be ready to ship to customers. Heijunka uses takt time as a way to control the production rate. You can use the takt to determine the product quantity and the pace at which customers buy the company's products. In back office settings, the takt timing is used to help determine how quickly customers purchase the company's products.
The heijunkabox allows production staff to visualise and plan the production process. You can also use the heijunka to help you visualize the production flow. The heijunka box is made up of rows and columns which represent each product type or component. The columns of boxes represent the different time periods, and the rows are for each product type.
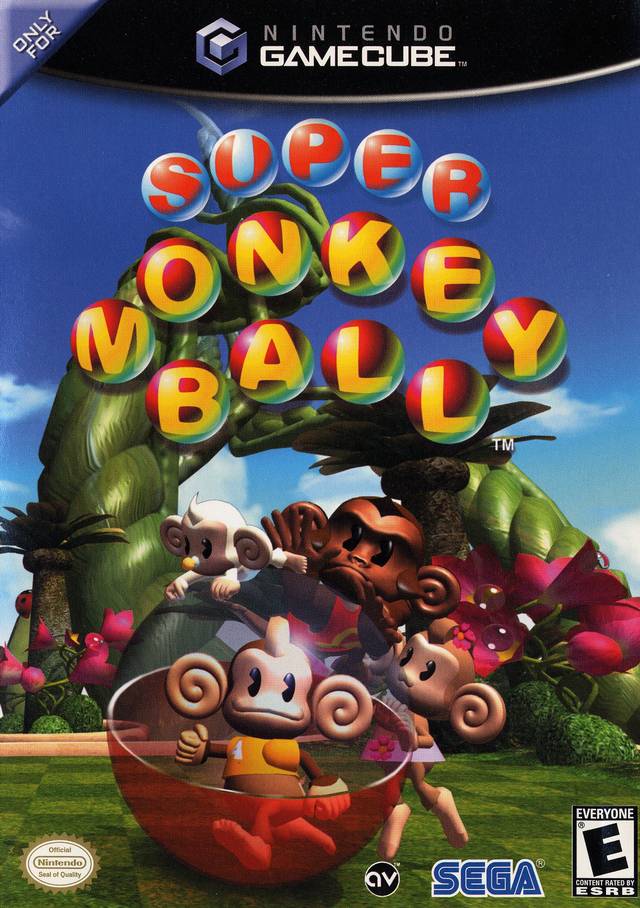
Heijunka Box can be used to manage production visuals. This tool allows you to see the relationships between component production and product production. This tool also shows the weekly production schedule. It can be used with kanban cards. These are colored cards that indicate the product needed for a particular production step. Kanban card are usually removed from the heijunka box within a given time frame and delivered to the designated production area.
FAQ
What is the job of a production plan?
Production planners ensure all aspects of the project are delivered within time and budget. They also ensure the quality of the product and service meets the client's requirements.
What are the 7 R's of logistics?
The acronym 7Rs of Logistics refers to the seven core principles of logistics management. It was published in 2004 by the International Association of Business Logisticians as part of their "Seven Principles of Logistics Management" series.
The acronym consists of the following letters:
-
Responsible - ensure that all actions taken are within legal requirements and are not harmful to others.
-
Reliable - have confidence in the ability to deliver on commitments made.
-
Be responsible - Use resources efficiently and avoid wasting them.
-
Realistic - Take into consideration all aspects of operations including cost-effectiveness, environmental impact, and other factors.
-
Respectful - Treat people fairly and equitably
-
Responsive - Look for ways to save time and increase productivity.
-
Recognizable is a company that provides customers with value-added solutions.
How can manufacturing avoid production bottlenecks
You can avoid bottlenecks in production by making sure that everything runs smoothly throughout the production cycle, from the moment you receive an order to the moment the product is shipped.
This includes planning for capacity requirements as well as quality control measures.
Continuous improvement techniques like Six Sigma are the best way to achieve this.
Six Sigma can be used to improve the quality and decrease waste in all areas of your company.
It seeks to eliminate variation and create consistency in your work.
What is the job of a logistics manger?
Logistics managers are responsible for ensuring that all goods arrive in perfect condition and on time. This is done using his/her knowledge of the company's products. He/she must also ensure sufficient stock to meet the demand.
What are the differences between these four types?
Manufacturing is the process by which raw materials are transformed into useful products through machines and processes. Manufacturing involves many activities, including designing, building, testing and packaging, shipping, selling, service, and so on.
Statistics
- [54][55] These are the top 50 countries by the total value of manufacturing output in US dollars for its noted year according to World Bank.[56] (en.wikipedia.org)
- (2:04) MTO is a production technique wherein products are customized according to customer specifications, and production only starts after an order is received. (oracle.com)
- In the United States, for example, manufacturing makes up 15% of the economic output. (twi-global.com)
- According to the United Nations Industrial Development Organization (UNIDO), China is the top manufacturer worldwide by 2019 output, producing 28.7% of the total global manufacturing output, followed by the United States, Japan, Germany, and India.[52][53] (en.wikipedia.org)
- According to a Statista study, U.S. businesses spent $1.63 trillion on logistics in 2019, moving goods from origin to end user through various supply chain network segments. (netsuite.com)
External Links
How To
How to Use the 5S to Increase Productivity In Manufacturing
5S stands in for "Sort", the "Set In Order", "Standardize", or "Separate". Toyota Motor Corporation was the first to develop the 5S approach in 1954. It allows companies to improve their work environment, thereby achieving greater efficiency.
This method has the basic goal of standardizing production processes to make them repeatable. This means that daily tasks such as cleaning and sorting, storage, packing, labeling, and packaging are possible. Through these actions, workers can perform their jobs more efficiently because they know what to expect from them.
Implementing 5S requires five steps. These are Sort, Set In Order, Standardize. Separate. And Store. Each step is a different action that leads to greater efficiency. For example, when you sort things, you make them easy to find later. When you set items in an order, you put items together. Then, after you separate your inventory into groups, you store those groups in containers that are easy to access. Finally, when you label your containers, you ensure everything is labeled correctly.
Employees need to reflect on how they do their jobs. Employees need to understand the reasons they do certain jobs and determine if there is a better way. They will need to develop new skills and techniques in order for the 5S system to be implemented.
The 5S method increases efficiency and morale among employees. As they begin to see improvements, they feel motivated to continue working towards the goal of achieving higher levels of efficiency.