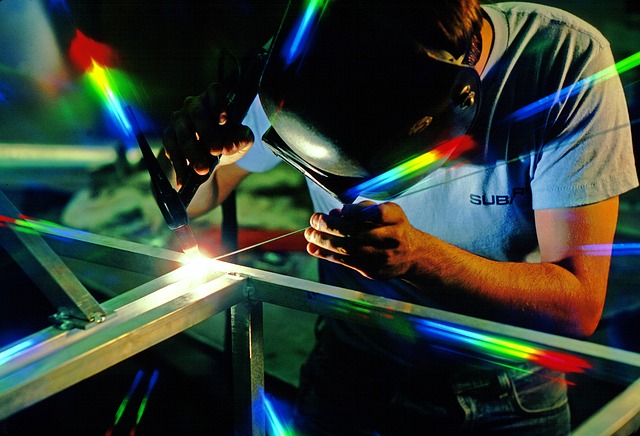
Lean manufacturing allows for a more efficient management system that helps reduce waste. It was inspired by the ideas of Henry Ford, Kiichiro Toyoda and others who presided over Toyota Motor Corporation before World War II. Manufacturing is not simply an assembly line. Lean manufacturing refers to it as a whole process. The five core principles of lean include eliminating waste, streamlining the process, creating knowledge, optimizing the whole and continuous improvement.
It is important to first identify what you are doing wrong. This can be accomplished using quantitative or qualitative techniques. You can check the price that your customers pay for your product. If the price you charge is more than the value that you provide, then you may have a problem.
Conducting a kaizen exercise is one way to find out how much waste is generated in a given process. It involves all employees working together to solve small problems in an incremental manner. Kaizen events can either be used on their own or in conjunction other lean tools.
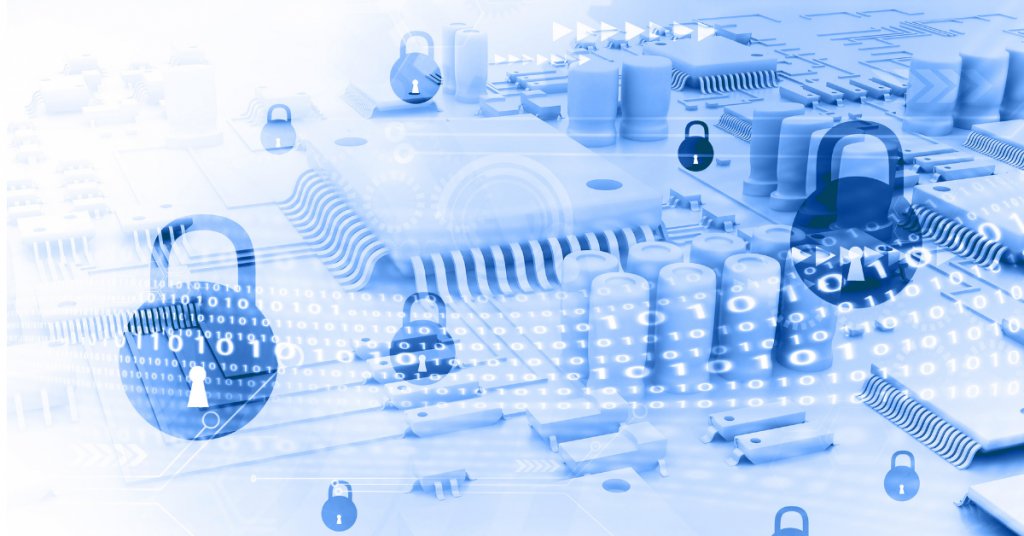
Value stream mapping is another way to identify production waste. VSM is a way for manufacturers to see the production steps and determine which are the most time-consuming.
Waste areas include inventory, waiting, overproduction, motion, and defects. To identify areas where improvement can be made, a lean team will map these areas. They could be part of the supply chain or in a production zone, or all throughout the process.
After identifying the waste, you are able to start implementing strategies for eliminating it. These strategies include creating cross-functional teams, reducing your workload and training your employees to become multi-skilled. You might want to implement technologies such just-in-time and cellular manufacturing, depending on your business. You can also employ other lean tools such as total productive maintenance and kanban management.
A system of standardized containers can be integrated to allow workers to count exact quantities. Standardized containers allow workers to easily detect whether food or other items are mixed in the products. Safety mats can be used near machine areas. These mats will stop the person from stepping on them.
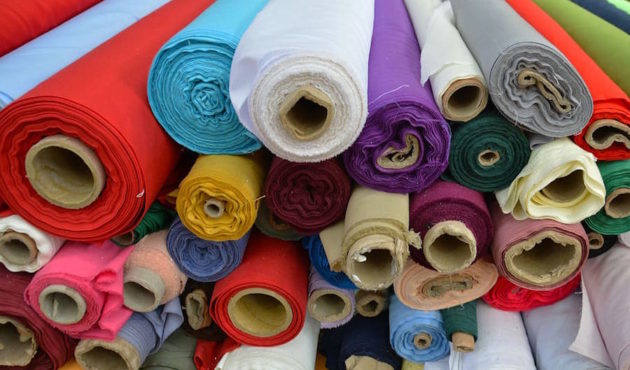
A strong organizational culture is essential for all lean initiatives. A strong organizational culture will include a clear understanding and communication skills as well as a long-term vision. It is crucial to create a sustainable improvement system in your company for its success.
A value stream map can be useful when you are looking for a machine. It is possible to create an inventory which includes future conditions of your products, raw material, and customer requirements. This information allows you to more accurately predict when and how much equipment you will need. Similarly, you can create a scheduling system to ensure you can fulfill orders on time.
You can make your company more efficient and help you achieve your objectives by using the five core principles of lean manufacture. There are many lean manufacturing websites that can help you learn more about the available techniques and resources.
FAQ
How can manufacturing excess production be decreased?
It is essential to find better ways to manage inventory to reduce overproduction. This would reduce the amount of time spent on unnecessary activities such as purchasing, storing, and maintaining excess stock. This would allow us to use our resources for more productive tasks.
You can do this by adopting a Kanban method. A Kanban board can be used to monitor work progress. Kanban systems allow work items to move through different states until they reach their final destination. Each state represents an individual priority level.
To illustrate, work can move from one stage or another when it is complete enough for it to be moved to a new stage. It is possible to keep a task in the beginning stages until it gets to the end.
This allows work to move forward and ensures that no work is missed. Managers can monitor the work being done by Kanban boards to see what is happening at any given time. This allows them to adjust their workflows based on real-time information.
Lean manufacturing can also be used to reduce inventory levels. Lean manufacturing works to eliminate waste throughout every stage of the production chain. Any product that isn't adding value can be considered waste. There are several types of waste that you might encounter:
-
Overproduction
-
Inventory
-
Packaging that is not necessary
-
Overstock materials
These ideas can help manufacturers improve efficiency and reduce costs.
What are the 4 types manufacturing?
Manufacturing is the process of transforming raw materials into useful products using machines and processes. It involves many different activities such as designing, building, testing, packaging, shipping, selling, servicing, etc.
What makes a production planner different from a project manger?
A production planner is more involved in the planning phase of the project than a project manger.
Statistics
- (2:04) MTO is a production technique wherein products are customized according to customer specifications, and production only starts after an order is received. (oracle.com)
- You can multiply the result by 100 to get the total percent of monthly overhead. (investopedia.com)
- Job #1 is delivering the ordered product according to specifications: color, size, brand, and quantity. (netsuite.com)
- According to a Statista study, U.S. businesses spent $1.63 trillion on logistics in 2019, moving goods from origin to end user through various supply chain network segments. (netsuite.com)
- Many factories witnessed a 30% increase in output due to the shift to electric motors. (en.wikipedia.org)
External Links
How To
Six Sigma: How to Use it in Manufacturing
Six Sigma refers to "the application and control of statistical processes (SPC) techniques in order to achieve continuous improvement." Motorola's Quality Improvement Department, Tokyo, Japan, developed it in 1986. Six Sigma's core idea is to improve the quality of processes by standardizing and eliminating defects. In recent years, many companies have adopted this method because they believe there is no such thing as perfect products or services. Six Sigma aims to reduce variation in the production's mean value. If you take a sample and compare it with the average, you will be able to determine how much of the production process is different from the norm. If you notice a large deviation, then it is time to fix it.
The first step toward implementing Six Sigma is understanding how variability works in your business. Once you have a good understanding of the basics, you can identify potential sources of variation. You'll also want to determine whether these variations are random or systematic. Random variations happen when people make errors; systematic variations are caused externally. Random variations would include, for example, the failure of some widgets to fall from the assembly line. However, if you notice that every time you assemble a widget, it always falls apart at exactly the same place, then that would be a systematic problem.
Once you've identified where the problems lie, you'll want to design solutions to eliminate those problems. You might need to change the way you work or completely redesign the process. Test them again once you've implemented the changes. If they don't work, you will need to go back to the drawing boards and create a new plan.