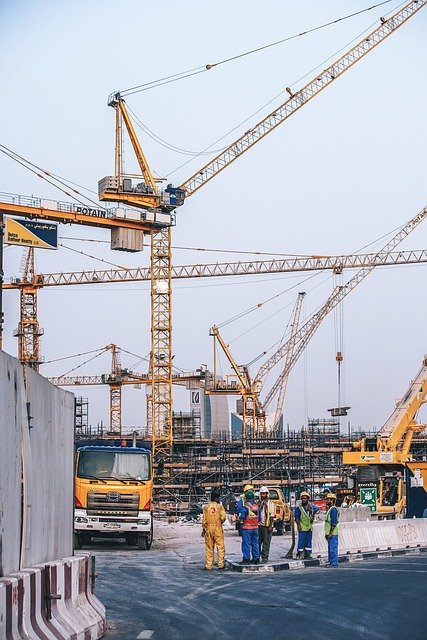
Mechatronics is an interdisciplinary field of engineering that combines electrical engineering and mechanical engineering. This combination is key to the development of advanced machines that are efficient. A typical mechatronic system consists of sensors, actuators, and electronics. It gathers signals from the environment and processes them to generate an output signal. This system is found in many products. Household items such as televisions and computers have mechatronic systems installed to make them work. The future of the electromechanical field is expected to include the development of mechatronic systems that are smarter and simpler.
The first electromechanical devices were used in early telegraphy. The first electromechanical device to transmit electrical signals was the Strowger Switch. These devices were extensively used in automated telephone networks in the United States by the middle of twentieth century. Nowadays, equipment with automated features is more common than ever. Solid-state electronics have replaced many electromechanical devices in many applications.
An Electro-mechanical Technician uses a combination of mechanical technology and electrical and electronic circuits in order to operate and maintain automated equipment. They might be involved in energy projects or maintenance of equipment used for deep-ocean exploration. They may also work on repairs. The Electro-Mechanical technician must be skilled in troubleshooting and mechanical skills. They should also be able work under pressure. They must also be able safely to use tools. Employers will find it a huge benefit to have them proficient in electrical and mechanical systems.
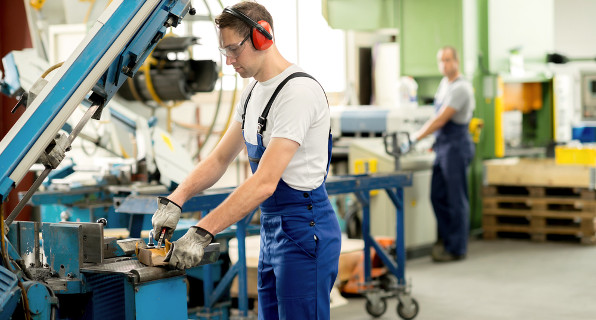
The diploma or certificate that Electro-mechanical Technicians can earn from technical or vocational schools is a diploma. They could also get an associate's/bachelor's in Electrical Engineering or Mechatronics. Certified Control Systems certification is another option that allows Electro-mechanical Technicians to demonstrate their professional competence.
Electro-Mechanical Technicians may also be called assemblers. They use assembly drawings and verbal instructions to assemble electronic or mechanical equipment. They may also work with production plans. These types are more likely to need transistors.
In the next years, mechatronics is likely to gain popularity. The society's need for high-functioning products and more efficient machines is the reason it has grown in popularity. There are many areas of potential in Mechatronics. These include the advancement of new technology such a particle electromechanics. Mechatronics combines both electrical engineering and computer sciences to find new solutions for problems. In addition, many large manufacturing companies are looking to develop new electronic-mechanical engineering technologies.
The field of mechanics can be very dynamic and always in flux. An Electromechanical Technician can specialize within the field of Mechatronics. This requires specialized understanding in electrical circuits and sensing engineering. These technicians are expected to use their specialized knowledge to design value-add products.
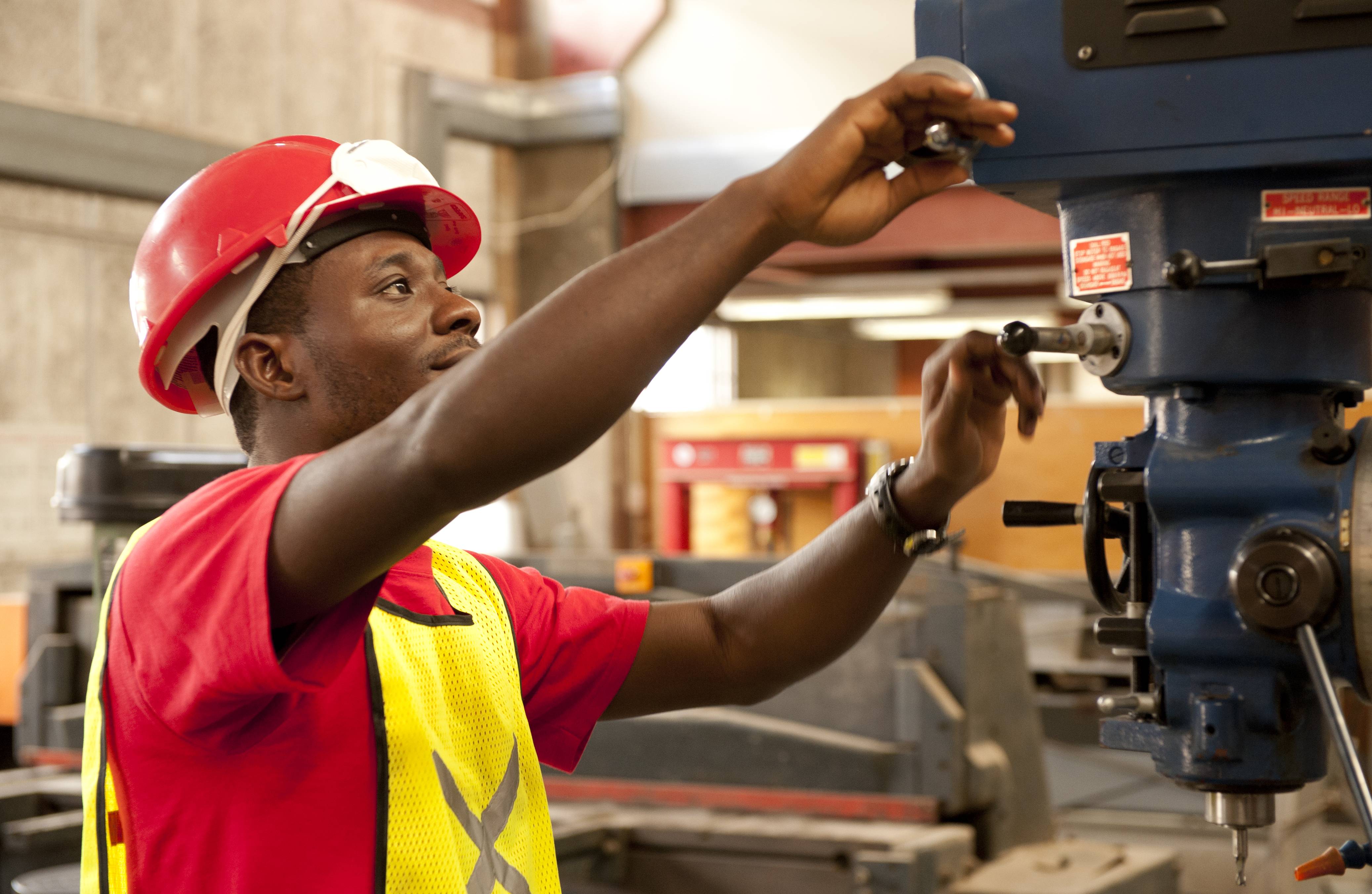
You can choose to specialize in electro-mechanical technicians, such as industrial maintenance, mechanics or maintenance and repair. These types of technicians are expected to continue to be in demand due to the rise of computer-control systems. Compensation is dependent on experience, geographic location and industry.
FAQ
Why automate your factory?
Modern warehousing is becoming more automated. With the rise of ecommerce, there is a greater demand for faster delivery times as well as more efficient processes.
Warehouses need to adapt quickly to meet changing needs. They must invest heavily in technology to do this. The benefits of automating warehouses are numerous. Here are some benefits of investing in automation
-
Increases throughput/productivity
-
Reduces errors
-
Improves accuracy
-
Safety enhancements
-
Eliminates bottlenecks
-
Allows companies to scale more easily
-
Increases efficiency of workers
-
This gives you visibility into what happens in the warehouse
-
Enhances customer experience
-
Improves employee satisfaction
-
Reducing downtime and increasing uptime
-
Ensures quality products are delivered on time
-
Removes human error
-
It helps ensure compliance with regulations
Why is logistics so important in manufacturing?
Logistics are an essential part of any business. They can help you achieve great success by helping you manage product flow from raw material to finished goods.
Logistics are also important in reducing costs and improving efficiency.
What skills is required for a production planner?
To become a successful production planner, you need to be organized, flexible, and able to multitask. It is also important to be able communicate with colleagues and clients.
Statistics
- [54][55] These are the top 50 countries by the total value of manufacturing output in US dollars for its noted year according to World Bank.[56] (en.wikipedia.org)
- You can multiply the result by 100 to get the total percent of monthly overhead. (investopedia.com)
- (2:04) MTO is a production technique wherein products are customized according to customer specifications, and production only starts after an order is received. (oracle.com)
- Many factories witnessed a 30% increase in output due to the shift to electric motors. (en.wikipedia.org)
- According to a Statista study, U.S. businesses spent $1.63 trillion on logistics in 2019, moving goods from origin to end user through various supply chain network segments. (netsuite.com)
External Links
How To
How to Use Lean Manufacturing in the Production of Goods
Lean manufacturing is an approach to management that aims for efficiency and waste reduction. It was developed by Taiichi Okono in Japan, during the 1970s & 1980s. TPS founder Kanji Takoda awarded him the Toyota Production System Award (TPS). The first book published on lean manufacturing was titled "The Machine That Changed the World" written by Michael L. Watkins and published in 1990.
Lean manufacturing can be described as a set or principles that are used to improve quality, speed and cost of products or services. It emphasizes the elimination of defects and waste throughout the value stream. Lean manufacturing is also known as just in time (JIT), zero defect total productive maintenance(TPM), and five-star (S). Lean manufacturing eliminates non-value-added tasks like inspection, rework, waiting.
Lean manufacturing is a way for companies to achieve their goals faster, improve product quality, and lower costs. Lean manufacturing is considered one of the most effective ways to manage the entire value chain, including suppliers, customers, distributors, retailers, and employees. Lean manufacturing can be found in many industries. Toyota's philosophy is a great example of this. It has helped to create success in automobiles as well electronics, appliances and healthcare.
Five fundamental principles underlie lean manufacturing.
-
Define Value - Identify the value your business adds to society and what makes you different from competitors.
-
Reduce waste - Stop any activity that isn't adding value to the supply chains.
-
Create Flow - Ensure work moves smoothly through the process without interruption.
-
Standardize and Simplify – Make processes as consistent, repeatable, and as simple as possible.
-
Build Relationships- Develop personal relationships with both internal as well as external stakeholders.
Lean manufacturing, although not new, has seen renewed interest in the economic sector since 2008. Many businesses have adopted lean production techniques to make them more competitive. According to some economists, lean manufacturing could be a significant factor in the economic recovery.
With many benefits, lean manufacturing is becoming more common in the automotive industry. These include higher customer satisfaction levels, reduced inventory levels as well as lower operating costs.
Any aspect of an enterprise can benefit from Lean manufacturing. However, it is particularly useful when applied to the production side of an organization because it ensures that all steps in the value chain are efficient and effective.
There are three types principally of lean manufacturing:
-
Just-in-Time Manufacturing: Also known as "pull systems", this type of lean manufacturing uses just-in-time manufacturing (JIT). JIT means that components are assembled at the time of use and not manufactured in advance. This approach is designed to reduce lead times and increase the availability of components. It also reduces inventory.
-
Zero Defects Manufacturing - ZDM: ZDM focuses its efforts on making sure that no defective units leave a manufacturing facility. Repairing a part that is damaged during assembly should be done, not scrapping. This applies to finished products, which may need minor repairs before they are shipped.
-
Continuous Improvement (CI), also known as Continuous Improvement, aims at improving the efficiency of operations through continuous identification and improvement to minimize or eliminate waste. Continuous improvement refers to continuous improvement of processes as well people and tools.