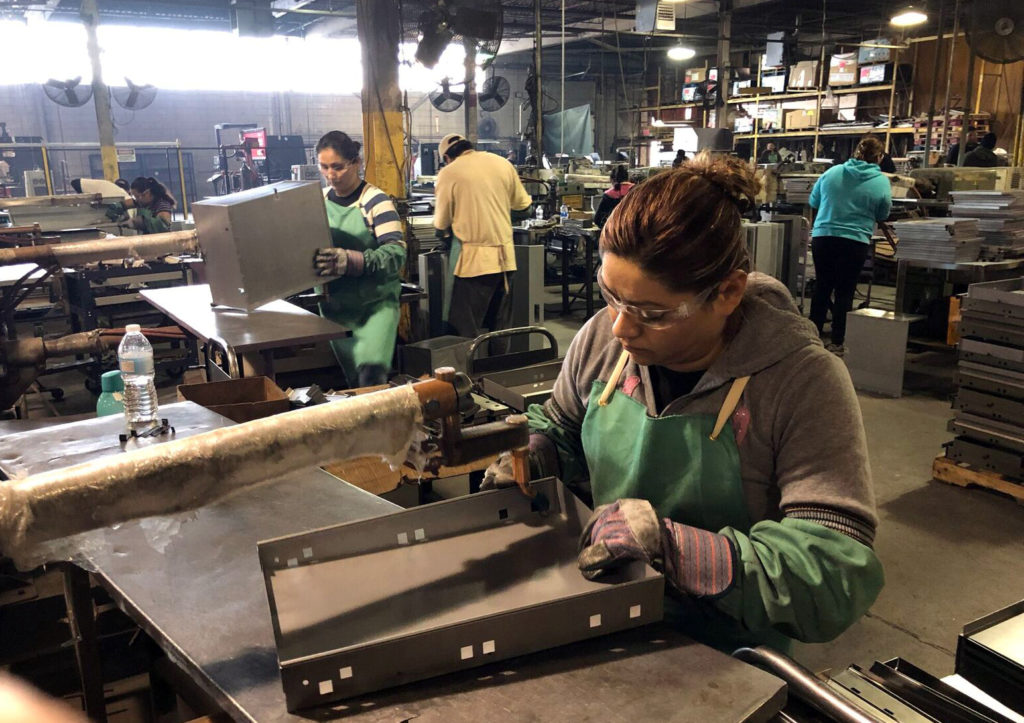
There are many jobs available in additive manufacture, no matter if you are a seasoned professional and/or aspiring newcomer. McKinsey has projected that the economic impact from additive manufacturing will be between $100 billion and $250 billion by 2025. Those interested in the field should consider educational and career paths that will prepare them for the future.
Material scientist is one of the most popular careers in additive manufacturing. They are responsible for testing materials' properties and creating new materials. They may also develop post-processing protocols and conduct research into the future of 3D printing materials.
There are many types of material scientists. However, the average salary is $150,000. Most jobs require research and development while others require testing the mechanical properties. Others are more concerned with finding new applications in additive manufacturing.
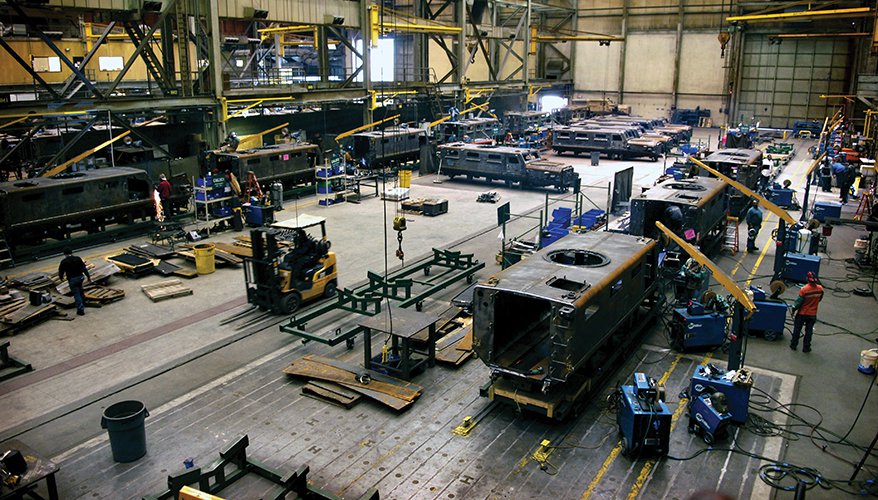
Over the last year, there has been a lot of industry growth. AT Kearney claims that additive manufacturing could result in five million jobs in the US over a ten-year period. There will be more companies that adopt this technology. This means there will be more demand for engineers, business professionals and marketing and sales specialists to support the business as well as the products it creates.
The main qualifications for a position in additive manufacturing are typically several years of experience, a bachelor's degree, and knowledge of the design software that is used in the industry. There may be different qualifications depending on the position. A broad education is not enough. The most important qualifications for jobs in additive manufacturing include data analysis and communication skills.
R&D are the most popular jobs in additive production. In fact, 58% employers anticipate hiring R&D positions in the next 12 months. These include industrial engineers who design additive manufacturing processes and design engineers who create 3D models.
The next most in-demand jobs are those that involve sales. These jobs require a bachelor's degree. However, some employers will consider candidates with advanced degrees. A variety of industries require sales personnel, including aerospace, automotive, and food.
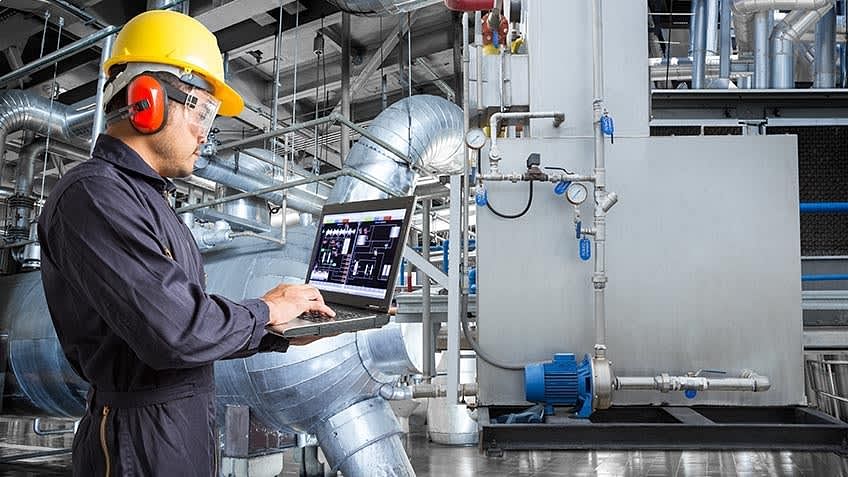
Software is another rapidly growing job category. Software development is a rapidly growing job category. This is not a linear career path. Employers are now looking for people who can think critically, solve complex problems, and have creativity. These skills can be developed and demonstrated to potential employers in order to land this job.
A number of job postings require a degree requiring computer science. Although not the most commonly taught path, this degree can help professionals acquire the skills they need to enter the field of additive manufacturing.
While the future for additive manufacturing is uncertain at this time, it's worth keeping an eye on its growth and considering whether this field is right. Joblist will help you locate and apply for opportunities in the industry if you are interested.
FAQ
What does the term manufacturing industries mean?
Manufacturing Industries refers to businesses that manufacture products. Consumers are those who purchase these products. These companies use various processes such as production, distribution, retailing, management, etc., to fulfill this purpose. They produce goods from raw materials by using machines and other machinery. This includes all types of manufactured goods, including food items, clothing, building supplies, furniture, toys, electronics, tools, machinery, vehicles, pharmaceuticals, medical devices, chemicals, and many others.
How can manufacturing excess production be decreased?
The key to reducing overproduction lies in developing better ways to manage inventory. This would reduce the time spent on unproductive activities like purchasing, storing and maintaining excess stock. By doing this, we could free up resources for other productive tasks.
This can be done by using a Kanban system. A Kanban board can be used to monitor work progress. A Kanban system allows work items to move through several states before reaching their final destination. Each state represents a different priority.
As an example, if work is progressing from one stage of the process to another, then the current task is complete and can be transferred to the next. A task that is still in the initial stages of a process will be considered complete until it moves on to the next stage.
This allows you to keep work moving along while making sure that no work gets neglected. Managers can monitor the work being done by Kanban boards to see what is happening at any given time. This information allows managers to adjust their workflow based off real-time data.
Lean manufacturing can also be used to reduce inventory levels. Lean manufacturing works to eliminate waste throughout every stage of the production chain. Any product that isn't adding value can be considered waste. The following are examples of common waste types:
-
Overproduction
-
Inventory
-
Packaging that is not necessary
-
Materials in excess
Manufacturers can reduce their costs and improve their efficiency by using these ideas.
What skills are required to be a production manager?
Being a production planner is not easy. You need to be organized and flexible. Communication skills are essential to ensure that you can communicate effectively with clients, colleagues, and customers.
What are the responsibilities for a manufacturing manager
A manufacturing manager has to ensure that all manufacturing processes work efficiently and effectively. They should also be aware and responsive to any company problems.
They must also be able to communicate with sales and marketing departments.
They should be informed about industry trends and be able make use of this information to improve their productivity and efficiency.
What is the importance of logistics in manufacturing?
Logistics are essential to any business. They help you achieve great results by helping you manage all aspects of product flow, from raw materials to finished goods.
Logistics plays a significant role in reducing cost and increasing efficiency.
Statistics
- Many factories witnessed a 30% increase in output due to the shift to electric motors. (en.wikipedia.org)
- You can multiply the result by 100 to get the total percent of monthly overhead. (investopedia.com)
- According to a Statista study, U.S. businesses spent $1.63 trillion on logistics in 2019, moving goods from origin to end user through various supply chain network segments. (netsuite.com)
- Job #1 is delivering the ordered product according to specifications: color, size, brand, and quantity. (netsuite.com)
- It's estimated that 10.8% of the U.S. GDP in 2020 was contributed to manufacturing. (investopedia.com)
External Links
How To
How to Use Six Sigma in Manufacturing
Six Sigma is defined as "the application of statistical process control (SPC) techniques to achieve continuous improvement." Motorola's Quality Improvement Department in Tokyo, Japan developed Six Sigma in 1986. Six Sigma is a method to improve quality through standardization and elimination of defects. Many companies have adopted this method in recent years. They believe there is no such thing a perfect product or service. Six Sigma aims to reduce variation in the production's mean value. This means that if you take a sample of your product, then measure its performance against the average, you can find out what percentage of the time the process deviates from the norm. If you notice a large deviation, then it is time to fix it.
Understanding the dynamics of variability within your business is the first step in Six Sigma. Once you understand that, it is time to identify the sources of variation. It is important to identify whether the variations are random or systemic. Random variations occur when people do mistakes. Symmetrical variations are caused due to factors beyond the process. If you make widgets and some of them end up on the assembly line, then those are considered random variations. You might notice that your widgets always fall apart at the same place every time you put them together.
Once you've identified the problem areas you need to find solutions. It might mean changing the way you do business or redesigning it entirely. To verify that the changes have worked, you need to test them again. If they don't work, you will need to go back to the drawing boards and create a new plan.