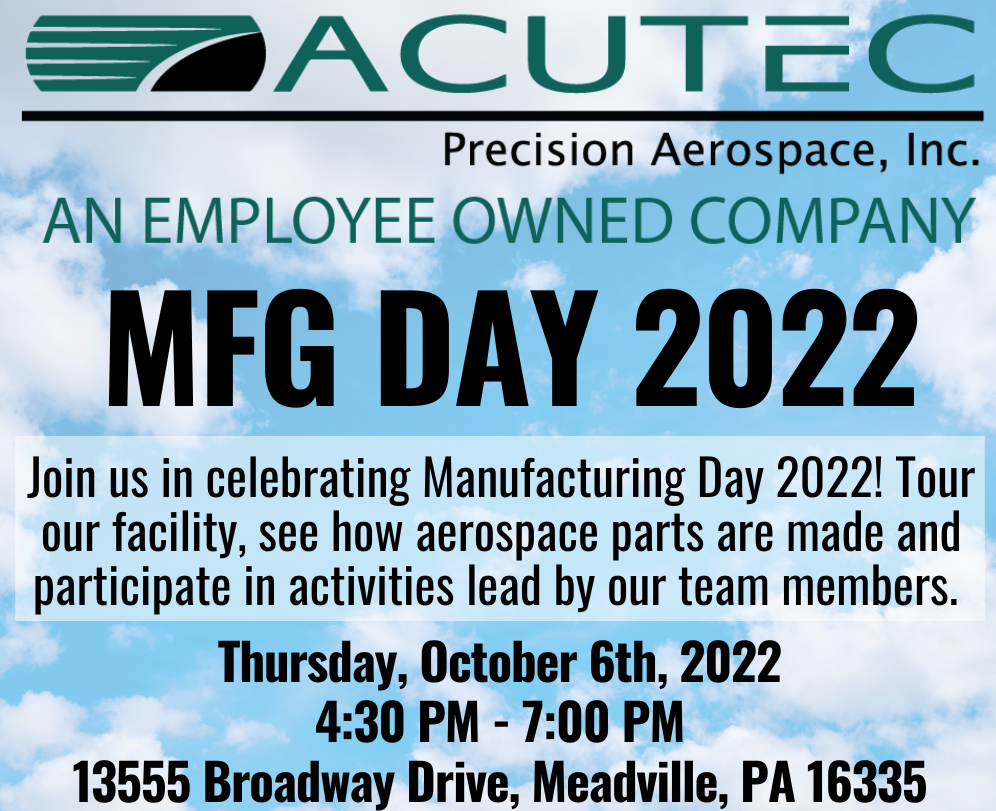
Lean 5 principles focus on eliminating waste. These principles encourage value stream mapping, which helps to identify opportunities for efficiency. To eliminate waste, it is important to distinguish between value-added waste (necessary), and non-value-added waste (unnecessary). By eliminating unnecessary steps, an efficient process is created that uses the least amount of time, energy, and materials. This allows you to produce high-quality products in a shorter time and keeps customers satisfied.
Value
The Value-of-Lean 5 principles help improve the flow and eliminate waste in manufacturing. It is possible to create smooth flows from production to shipping by eliminating steps that are not adding value. This eliminates inventory that is not needed and allows you to reduce your work and save time.
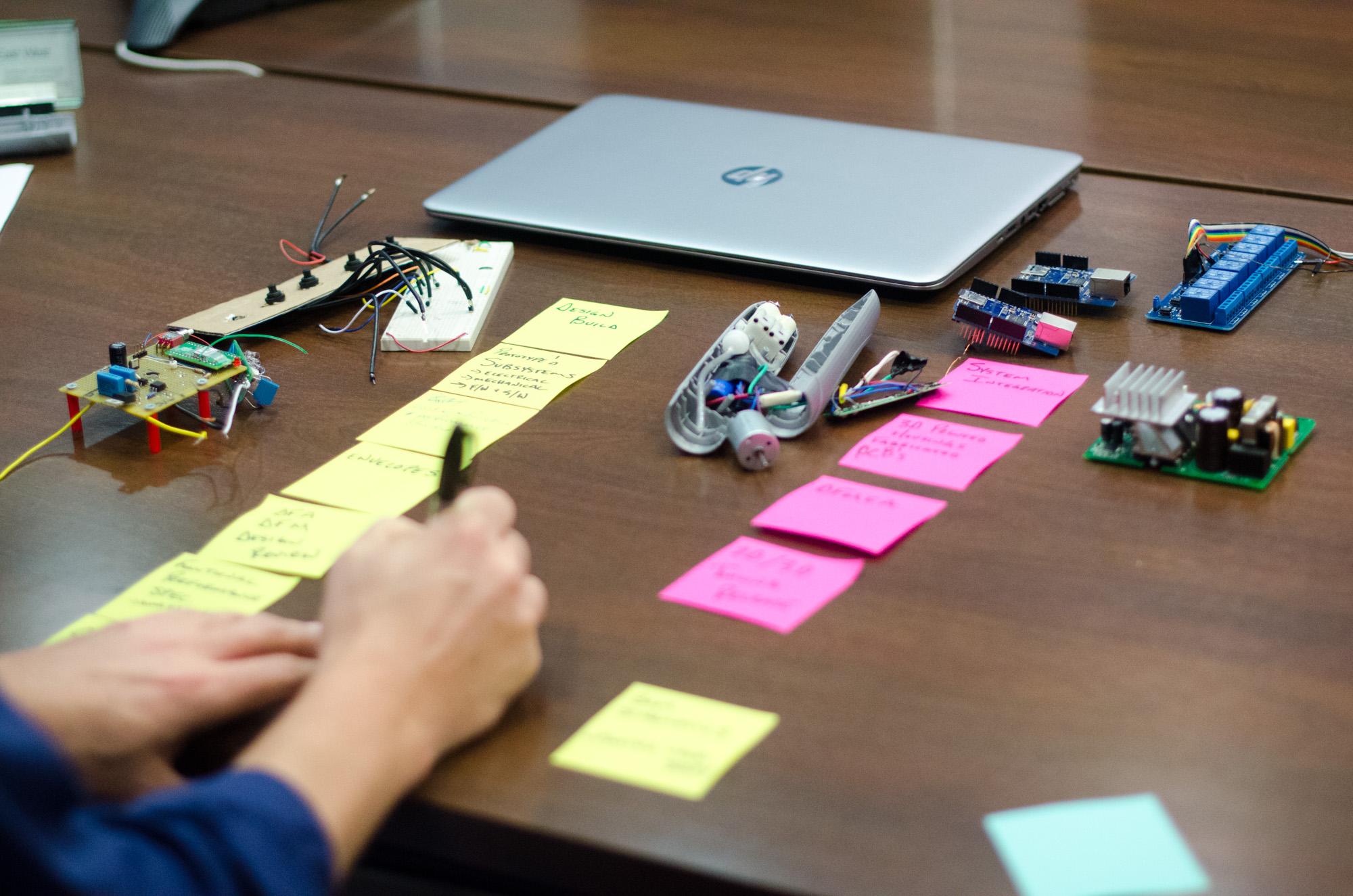
Value stream
The value stream in lean manufacturing is a technique to eliminate waste from manufacturing processes. This process maps each step in a process and identifies the essential elements. It also eliminates those elements that aren't necessary. The value stream takes into account the whole life cycle of a product - from the initial idea to the use of the product and its eventual disposal. This is the key to eliminating all waste. There are three types waste in a value stream.
Flow
The first principle of lean 5, Flow, is to identify and evaluate the customer's actual needs. This step is important in the design of new products and services because customers do not always express their needs clearly. Next, you need to identify the value stream. This refers to the set of activities needed for the project. This step is crucial to lean project management. It requires close collaboration between all project participants.
Pull
In a pull system, the process begins only when there is an order from a customer. An example: A pizza place would not make extra pizzas, they only would produce food when they received a customer's order. If they didn't, they would waste time and resources as well as their ingredients.
Perfection
One of the five lean principles is perfection. Perfection is a state of being complete, exact, consistent. Although perfection is possible, it is not a realistic goal. The idea behind this concept is to promote continuous improvement. In the process, organizations achieve a higher level of performance.
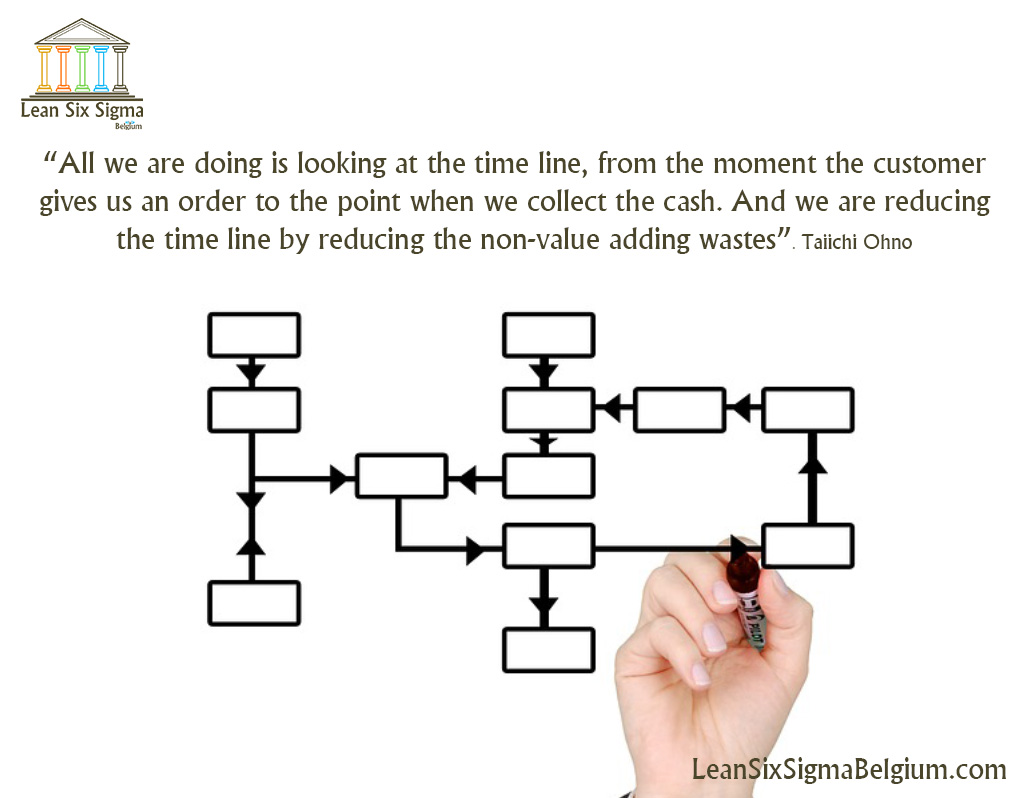
Collaboration between stakeholders
Lean project management is all about stakeholder collaboration. Collaboration between project team members is essential to solving problems and increasing project value. Teams need to identify potential problems and areas for improvement during the planning stage. The doing phase involves gathering data to help them find solutions. Execution is not the main focus. The team should also consider the organizational structure for collaboration.
FAQ
What are the responsibilities of a production planner
Production planners ensure all aspects of the project are delivered within time and budget. They also ensure that the product/service meets the client’s needs.
How can manufacturing excess production be decreased?
The key to reducing overproduction lies in developing better ways to manage inventory. This would decrease the time that is spent on inefficient activities like purchasing, storing, or maintaining excess stock. By doing this, we could free up resources for other productive tasks.
One way to do this is to adopt a Kanban system. A Kanban board is a visual display used to track work in progress. Work items are moved through various states to reach their destination in a Kanban system. Each state has a different priority level.
If work is moving from one stage to the other, then the current task can be completed and moved on to the next. If a task is still in its beginning stages, it will continue to be so until it reaches the end.
This keeps work moving and ensures no work is lost. Managers can see how much work has been done and the status of each task at any time with a Kanban Board. This information allows managers to adjust their workflow based off real-time data.
Lean manufacturing is another option to control inventory levels. Lean manufacturing works to eliminate waste throughout every stage of the production chain. Anything that does nothing to add value to a product is waste. Here are some examples of common types.
-
Overproduction
-
Inventory
-
Packaging not required
-
Excess materials
These ideas can help manufacturers improve efficiency and reduce costs.
Why automate your warehouse
Modern warehouses have become more dependent on automation. E-commerce has brought increased demand for more efficient and quicker delivery times.
Warehouses need to adapt quickly to meet changing needs. To do so, they must invest heavily in technology. The benefits of automating warehouses are numerous. These are just a few reasons to invest in automation.
-
Increases throughput/productivity
-
Reduces errors
-
Improves accuracy
-
Boosts safety
-
Eliminates bottlenecks
-
This allows companies to scale easily
-
Makes workers more efficient
-
Provides visibility into everything that happens in the warehouse
-
Enhances customer experience
-
Improves employee satisfaction
-
Minimizes downtime and increases uptime
-
Quality products delivered on time
-
Human error can be eliminated
-
Helps ensure compliance with regulations
What are the 7 Rs of logistics?
The acronym 7Rs of Logistics refers to the seven core principles of logistics management. It was developed by International Association of Business Logisticians (IABL), and published as part of their "Seven Principles of Logistics Management Series" in 2004.
The following letters make up the acronym:
-
Responsible - ensure that all actions taken are within legal requirements and are not harmful to others.
-
Reliable - You can have confidence that you will fulfill your promises.
-
Reasonable - use resources efficiently and don't waste them.
-
Realistic - consider all aspects of operations, including cost-effectiveness and environmental impact.
-
Respectful – Treat others fairly and equitably.
-
You are resourceful and look for ways to save money while increasing productivity.
-
Recognizable provides value-added products and services to customers
Is automation important for manufacturing?
Automation is essential for both manufacturers and service providers. It enables them to provide services faster and more efficiently. It helps them to lower costs by reducing human errors, and improving productivity.
How can I find out more about manufacturing?
Experience is the best way for you to learn about manufacturing. You can also read educational videos or take classes if this isn't possible.
What is production planning?
Production Planning is the creation of a plan to cover all aspects, such as scheduling, budgeting. Location, crew, equipment, props and other details. This document ensures that everything is prepared and available when you are ready for shooting. It should also provide information about how best to produce the best results while on set. This includes location information, crew details, equipment specifications, and casting lists.
The first step is to decide what you want. You might have an idea of where you want to film, or you may have specific locations or sets in mind. Once you've identified the locations and scenes you want to use, you can begin to plan what elements you need for each scene. Perhaps you have decided that you need to buy a car but aren't sure which model. To narrow your options, you can search online for available models.
After you have selected the car you want, you can begin to think about additional features. What about additional seating? Or maybe you just need someone to push the car around. You might want to change your interior color from black and white. These questions will help to determine the style and feel of your car. The type of shots that you are looking for is another thing to consider. Are you going to be shooting close-ups? Or wide angles? Maybe you want to show your engine or the steering wheel. This will allow you to determine the type of car you want.
Once you have determined all of the above, you can move on to creating a schedule. The schedule will show you when to begin shooting and when to stop. The schedule will show you when to get there, what time to leave, and when to return home. It will help everyone know exactly what they have to do and when. Hire extra staff by booking them ahead of time. You should not hire anyone who doesn't show up because of your inaction.
Also, consider how many days you will be filming your schedule. Some projects may only take a couple of days, while others could last for weeks. You should consider whether you will need more than one shot per week when creating your schedule. Shooting multiple takes over the same location will increase costs and take longer to complete. If you are unsure if you need multiple takes, it is better to err on the side of caution and shoot fewer takes rather than risk wasting money.
Budget setting is another important aspect in production planning. A realistic budget will help you work within your means. Keep in mind that you can always reduce your budget if you face unexpected difficulties. It is important to not overestimate how much you will spend. You will end up spending less money if you underestimate the cost of something.
Production planning is a very detailed process, but once you understand how everything works together, it becomes easier to plan future projects.
Statistics
- In the United States, for example, manufacturing makes up 15% of the economic output. (twi-global.com)
- In 2021, an estimated 12.1 million Americans work in the manufacturing sector.6 (investopedia.com)
- (2:04) MTO is a production technique wherein products are customized according to customer specifications, and production only starts after an order is received. (oracle.com)
- According to a Statista study, U.S. businesses spent $1.63 trillion on logistics in 2019, moving goods from origin to end user through various supply chain network segments. (netsuite.com)
- Many factories witnessed a 30% increase in output due to the shift to electric motors. (en.wikipedia.org)
External Links
How To
How to Use the Just In Time Method in Production
Just-in-time (JIT) is a method that is used to reduce costs and maximize efficiency in business processes. It's the process of obtaining the right amount and timing of resources when you need them. This means that only what you use is charged to your account. The term was first coined by Frederick Taylor, who developed his theory while working as a foreman in the early 1900s. After observing how workers were paid overtime for late work, he realized that overtime was a common practice. He decided to ensure workers have enough time to do their jobs before starting work to improve productivity.
JIT is a way to plan ahead and make sure you don't waste any money. It is important to look at your entire project from beginning to end and ensure that you have enough resources to handle any issues that may arise. You will have the resources and people to solve any problems you anticipate. You won't have to pay more for unnecessary items.
There are many JIT methods.
-
Demand-driven JIT: This is a JIT that allows you to regularly order the parts/materials necessary for your project. This will allow for you to track the material that you have left after using it. This will allow you to calculate how long it will take to make more.
-
Inventory-based: This is a type where you stock the materials required for your projects in advance. This allows you to predict how much you can expect to sell.
-
Project-driven: This method allows you to set aside enough funds for your project. Knowing how much money you have available will help you purchase the correct amount of materials.
-
Resource-based JIT: This is the most popular form of JIT. Here, you allocate certain resources based on demand. If you have many orders, you will assign more people to manage them. If you don't receive many orders, then you'll assign fewer employees to handle the load.
-
Cost-based: This is similar to resource-based, except that here you're not just concerned about how many people you have but how much each person costs.
-
Price-based: This approach is very similar to the cost-based method except that you don't look at individual workers costs but the total cost of the company.
-
Material-based: This is quite similar to cost-based, but instead of looking at the total cost of the company, you're concerned with how much raw materials you spend on average.
-
Time-based: This is another variation of resource-based JIT. Instead of worrying about how much each worker costs, you can focus on how long the project takes.
-
Quality-based: This is yet another variation of resource-based JIT. Instead of thinking about how much each employee costs or how long it takes to manufacture something, you think about how good the quality of your product is.
-
Value-based JIT is the newest form of JIT. You don't worry about whether the products work or if they meet customer expectations. Instead, your goal is to add value to the market.
-
Stock-based: This is an inventory-based method that focuses on the actual number of items being produced at any given time. It's useful when you want maximum production and minimal inventory.
-
Just-intime planning (JIT), is a combination JIT/sales chain management. It is the process of scheduling components' delivery as soon as they have been ordered. It reduces lead times and improves throughput.