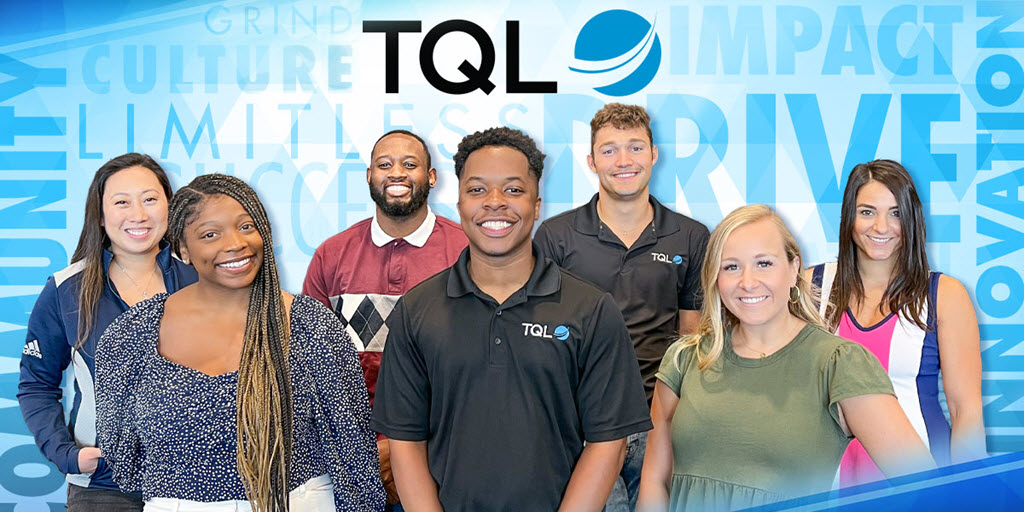
Flow is the state in which all the steps of a production line follow each other seamlessly without interruption. Each step adds value and the goods flow freely through the production process. Production of a specified quantity of stock is planned in many companies to make sure that production orders are met as efficiently as possible. In Lean Manufacturing, this is called "push production". Here are the key elements that make flow work:
Manufacturing just-in-time
When lean manufacturing was first introduced to the U.S. in the late 1970s, "just-in-time" manufacturing was the dominant paradigm. The concept isn't the best way to run a business, but it has its advantages. The process of reducing costs and increasing efficiency requires many new skills and mindsets. It is worth the effort if you are to reap all of its benefits.
Among the most important aspects of just-in-time manufacturing is standardizing procedures and working with smaller lots. It is crucial to have a well-planned facility layout in order to promote a just-in time mindset. Cellular manufacturing is one example of a way to improve production flow. You can arrange workstations and parts bins in cells to facilitate smoother flow of material. Long changeover times should be avoided by just-in time manufacturers.
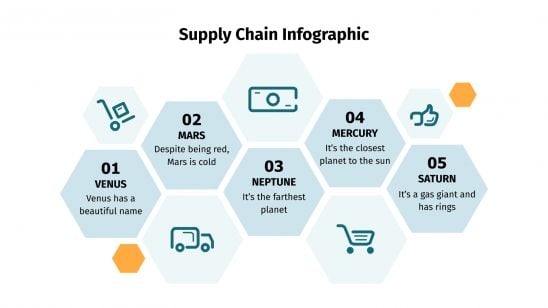
Standardized work
To apply lean manufacturing to manufacturing processes, you must first develop standardized work. This system of work focuses on the workers and what they must do to create a product or service. This refers to the ongoing improvement of the system through kaizen. The cell leader is responsible to update standardized work documents as soon as takt time changes. Standardized documentation serves as a foundation for improvement activities.
Organizations can improve their productivity as well as service quality by having standard work processes. They help to reduce product development and human error. This helps organizations to resolve problems more quickly because people understand the process better. This enables the organization to implement continuous improvement and increase its customer satisfaction. Once standardized, it is not difficult to implement these processes in a company. A mission statement is an important part of any company.
Continuous improvement
Lean principles promote continual improvement, resulting in a range of benefits. These benefits are usually additive. However, they all have one common thread: improved productivity, lower costs, shorter lead times and reduced lead times. The ultimate goal of continuous improvement is to increase value creation. How does continuous improvement work? This article will outline some of the many benefits of continuous optimization. It's simple: Continuous Improvement helps companies save money.
Continuous improvement focuses on small, incremental improvements and not large-scale changes. Although individual improvements are small and seem insignificant, the total improvement is substantial. Slow improvements are more effective than large leaps. In a lean manufacturing environment, continuous improvement focuses on alignment of goals, allowing the business to maximize productivity and profitability. Continuous improvement methods can streamline production and make it easier for all involved to reach a common goal.
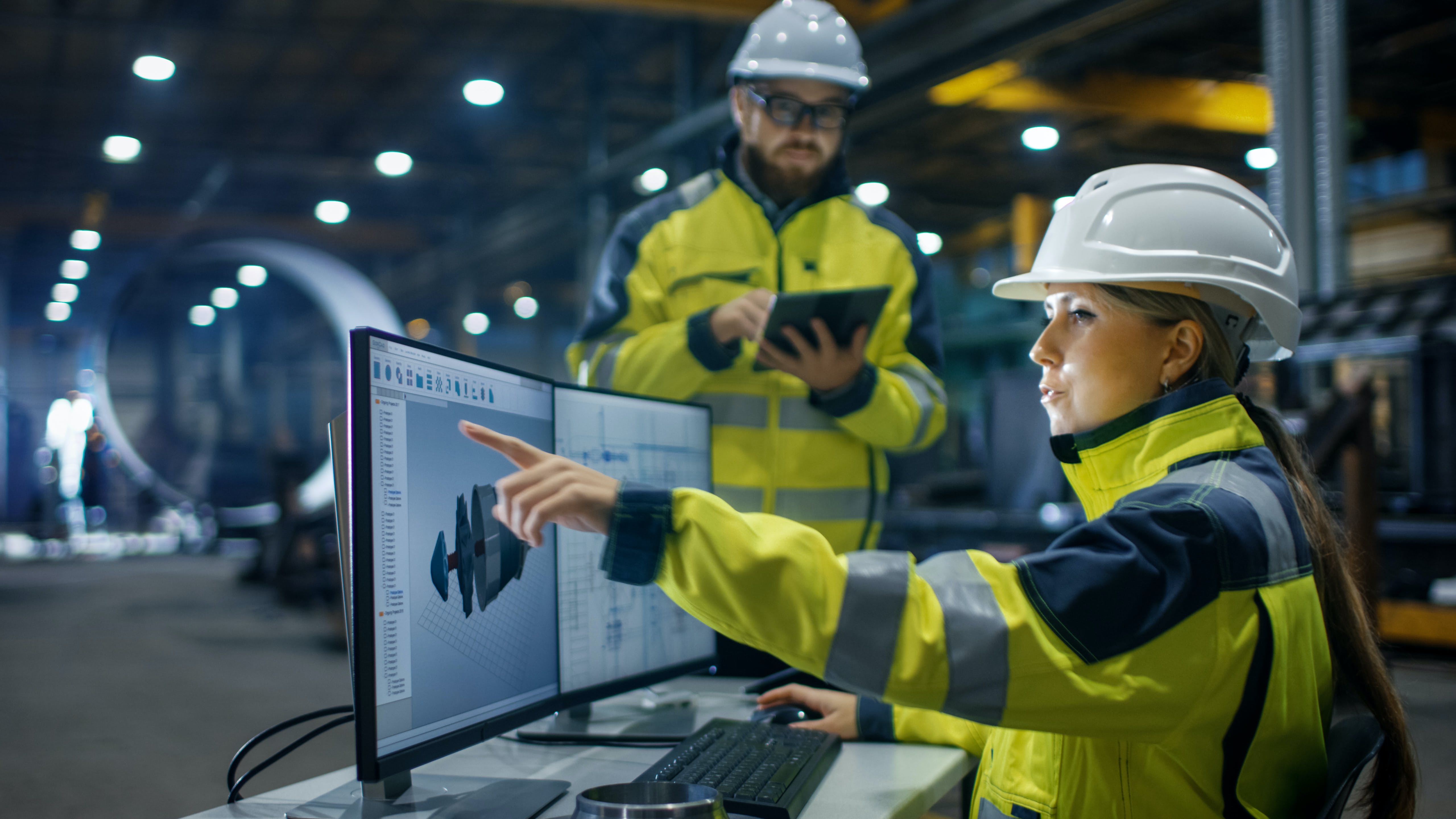
Kaizen
Kaizen in lean manufacturing focuses on waste elimination. Sometimes it can improve production yield, decrease lead times, and improve quality. To solve the problem, employees are divided into teams to work in specific roles. The creation of a flow map that demonstrates the value of the process is often the first step of a kaizen project. The team then conducts an analysis of time and other relevant operations. This process is repeated until every step has been improved. The overall process is then more efficient.
One example: A manufacturing plant may choose to buy a new forklift after identifying inefficiencies. The operator may be able to move inventory around faster, making loading and unloading easier. Similar to the value stream it's a map showing all the processes that go into creating products and services. Five S's were used to increase workplace productivity and employee productivity during the mapping process. There are seven types muda. Each one focuses on an aspect of a manufacturing process.
FAQ
How can manufacturing efficiency improved?
First, identify the factors that affect production time. Next, we must find ways to improve those factors. If you aren't sure where to begin, think about the factors that have the greatest impact on production time. Once you identify them, look for solutions.
What is the difference between Production Planning, Scheduling and Production Planning?
Production Planning (PP) refers to the process of determining how much production is needed at any given moment. This is accomplished by forecasting the demand and identifying production resources.
Scheduling involves the assignment of dates and times to tasks in order to complete them within the timeframe.
What are manufacturing and logistics?
Manufacturing refers the process of producing goods from raw materials through machines and processes. Logistics covers all aspects involved in managing supply chains, including procurement and production planning. Manufacturing and logistics can often be grouped together to describe a larger term that covers both the creation of products, and the delivery of them to customers.
What is production management?
Production Planning includes planning for all aspects related to production. This document will ensure everything is in order and ready to go when you need it. You should also have information to ensure the best possible results on set. This includes shooting schedules, locations, cast lists, crew details, and equipment requirements.
The first step is to decide what you want. You may have decided where to shoot or even specific locations you want to use. Once you have identified your locations and scenes, you can start working out which elements you require for each scene. Perhaps you have decided that you need to buy a car but aren't sure which model. You could look online for cars to see what options are available, and then narrow down your choices by selecting between different makes or models.
Once you have found the right car, you can start thinking about extras. What about additional seating? Or perhaps you need someone walking around the back of the car? Maybe you want to change the interior color from black to white? These questions will help you determine the exact look and feel of your car. The type of shots that you are looking for is another thing to consider. Are you going to be shooting close-ups? Or wide angles? Maybe you want to show the engine and the steering wheel. These things will help you to identify the car that you are looking for.
Once you have established all the details, you can create a schedule. A schedule will tell you when you need to start shooting and when you need to finish. You will need to know when you have to be there, what time you have to leave and when your return home. It will help everyone know exactly what they have to do and when. You can also make sure to book extra staff in advance if you have to hire them. You don't want to hire someone who won't show up because he didn't know.
You will need to factor in the days that you have to film when creating your schedule. Some projects can be completed in a matter of days or weeks. Others may take several days. When you are creating your schedule, you should always keep in mind whether you need more than one shot per day or not. Multiplying takes in the same area will result both in increased costs and a longer time. You can't be certain if you will need multiple takes so it is better not to shoot too many.
Budgeting is another crucial aspect of production plan. Setting a realistic budget is essential as it will allow you to work within your means. Remember that you can always reduce the budget later on if you run into unforeseen problems. However, you shouldn't overestimate the amount of money you will spend. Underestimating the cost will result in less money after you have paid for other items.
Production planning is a complicated process. But once you understand how everything works together, it becomes much easier to plan future project.
How is a production manager different from a producer planner?
The difference between a product planner and project manager is that a planer is typically the one who organizes and plans the entire project. A production planner, however, is mostly involved in the planning stages.
What does the term manufacturing industries mean?
Manufacturing Industries is a group of businesses that produce goods for sale. These products are sold to consumers. These companies employ many processes to achieve this purpose, such as production and distribution, retailing, management and so on. They create goods from raw materials, using machines and various other equipment. This includes all types if manufactured goods.
What are the responsibilities of a production planner
Production planners make sure that every aspect of the project is delivered on-time, within budget, and within schedule. They also ensure that the product/service meets the client’s needs.
Statistics
- You can multiply the result by 100 to get the total percent of monthly overhead. (investopedia.com)
- Job #1 is delivering the ordered product according to specifications: color, size, brand, and quantity. (netsuite.com)
- [54][55] These are the top 50 countries by the total value of manufacturing output in US dollars for its noted year according to World Bank.[56] (en.wikipedia.org)
- According to a Statista study, U.S. businesses spent $1.63 trillion on logistics in 2019, moving goods from origin to end user through various supply chain network segments. (netsuite.com)
- In the United States, for example, manufacturing makes up 15% of the economic output. (twi-global.com)
External Links
How To
Six Sigma in Manufacturing
Six Sigma is defined by "the application SPC (statistical process control) techniques to achieve continuous improvements." Motorola's Quality Improvement Department, Tokyo, Japan, developed it in 1986. Six Sigma's main goal is to improve process quality by standardizing processes and eliminating defects. This method has been adopted by many companies in recent years as they believe there are no perfect products or services. Six Sigma's main objective is to reduce variations from the production average. If you take a sample and compare it with the average, you will be able to determine how much of the production process is different from the norm. If the deviation is excessive, it's likely that something needs to be fixed.
Understanding the dynamics of variability within your business is the first step in Six Sigma. Once you have a good understanding of the basics, you can identify potential sources of variation. It is important to identify whether the variations are random or systemic. Random variations are caused when people make mistakes. While systematic variations are caused outside of the process, they can occur. Random variations would include, for example, the failure of some widgets to fall from the assembly line. It would be considered a systematic problem if every widget that you build falls apart at the same location each time.
Once you've identified the problem areas you need to find solutions. The solution could involve changing how you do things, or redesigning your entire process. After implementing the new changes, you should test them again to see if they worked. If they don’t work, you’ll need to go back and rework the plan.