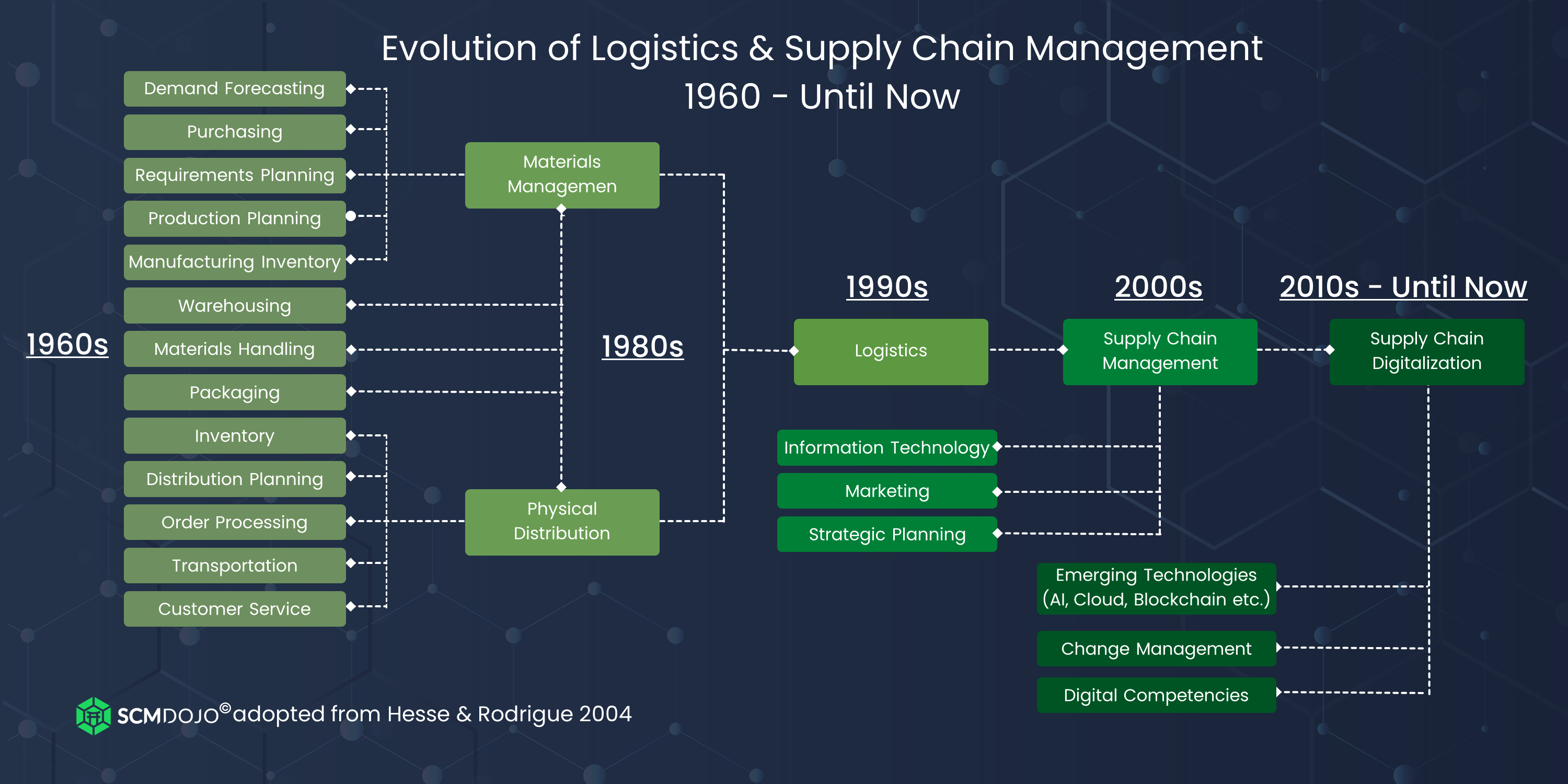
If you're interested in a career as a maintenance engineer, you need to have the right qualifications. Here are some of these certifications and the expected earnings. Maintenance engineers are a job that is perfect for those who have a keen eye for detail. They are responsible for maintaining the building's infrastructure and ensuring that it operates at its best.
Qualifications to be a Maintenance Engineer
A few key things to consider when considering a career in maintenance engineering. While a high school diploma will provide the foundational skills you need, you can also consider taking a college course in engineering. You will benefit from courses in physics, chemistry, math, and any other sciences. Work experience will also be helpful. A technical school may be an option depending on the needs and interests of your company.
The maintenance engineer is responsible for the maintenance of machinery and equipment, as well as systems, infrastructures, and systems. Their job is keep industrial machinery in operation as efficiently possible. They are responsible for ensuring that spare parts and supplies are available. Some jobs in this field require shift work, particularly those involved in manufacturing. Depending on the type of work, maintenance engineers can advance to management positions or even pursue other areas of employment in related industries. After they have gained experience, they may be able to start their own business.
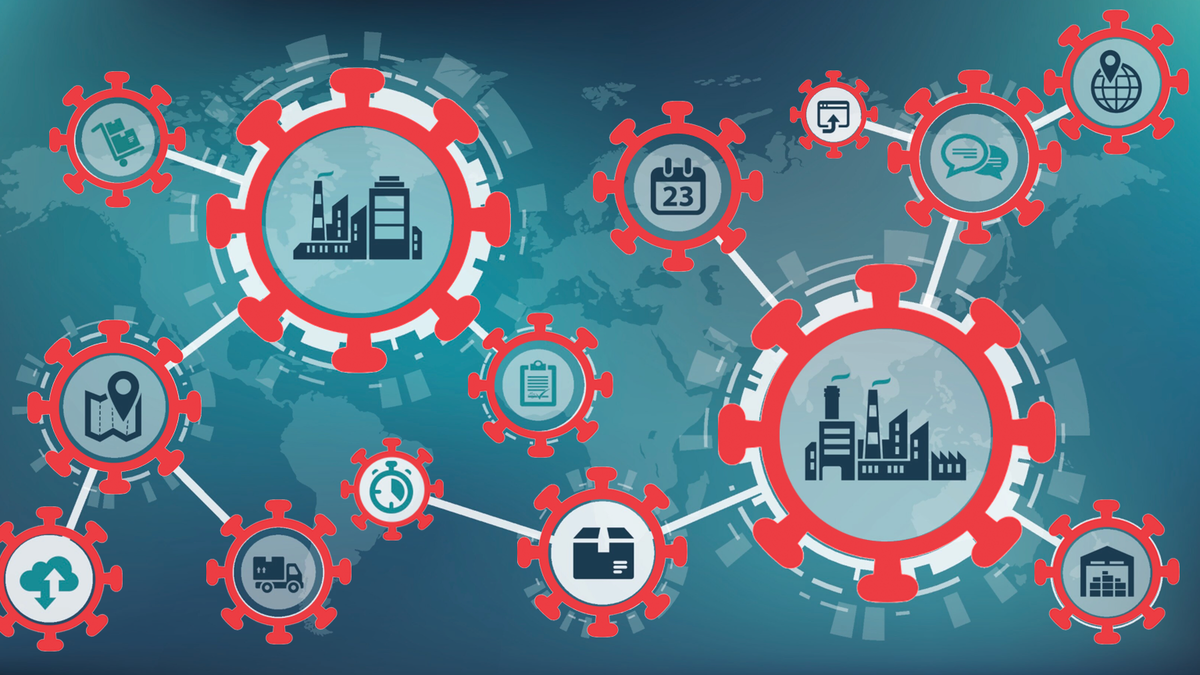
Maintenance engineers are paid between PS20,000 and PS25,000 in an average year. Salaries can vary depending on the size and industry of the organization. A maintenance engineer can also progress to management positions, which require leadership skills. The Chartered status could also aid in career advancement.
Certifications are required
Maintenance engineers may require multiple certifications. These certifications may be specific to a certain system, or they may pertain to the handling of hazardous materials. There are several levels of professional certification offered by the International Maintenance Institute. These include certifications for Certified Technicians and Certified Maintenance Managers.
You should first think about your education history if you want to become a maintenance engineer. While most certification providers don't require specific educational qualifications, some recommend a high school diploma or GED. This is the minimum requirement for most employers and recruiters. A certification can be obtained without a degree if the applicant has previous work experience.
Although a bachelor's degree does not necessarily mean you can become a maintenance engineer or vice versa, a degree in a relevant field will make you stand out among the rest. A degree in electrical engineering, mechanical engineering, or facilities management may be useful. Even if an engineering degree is not required, it's possible to get work as a maintenance technician.
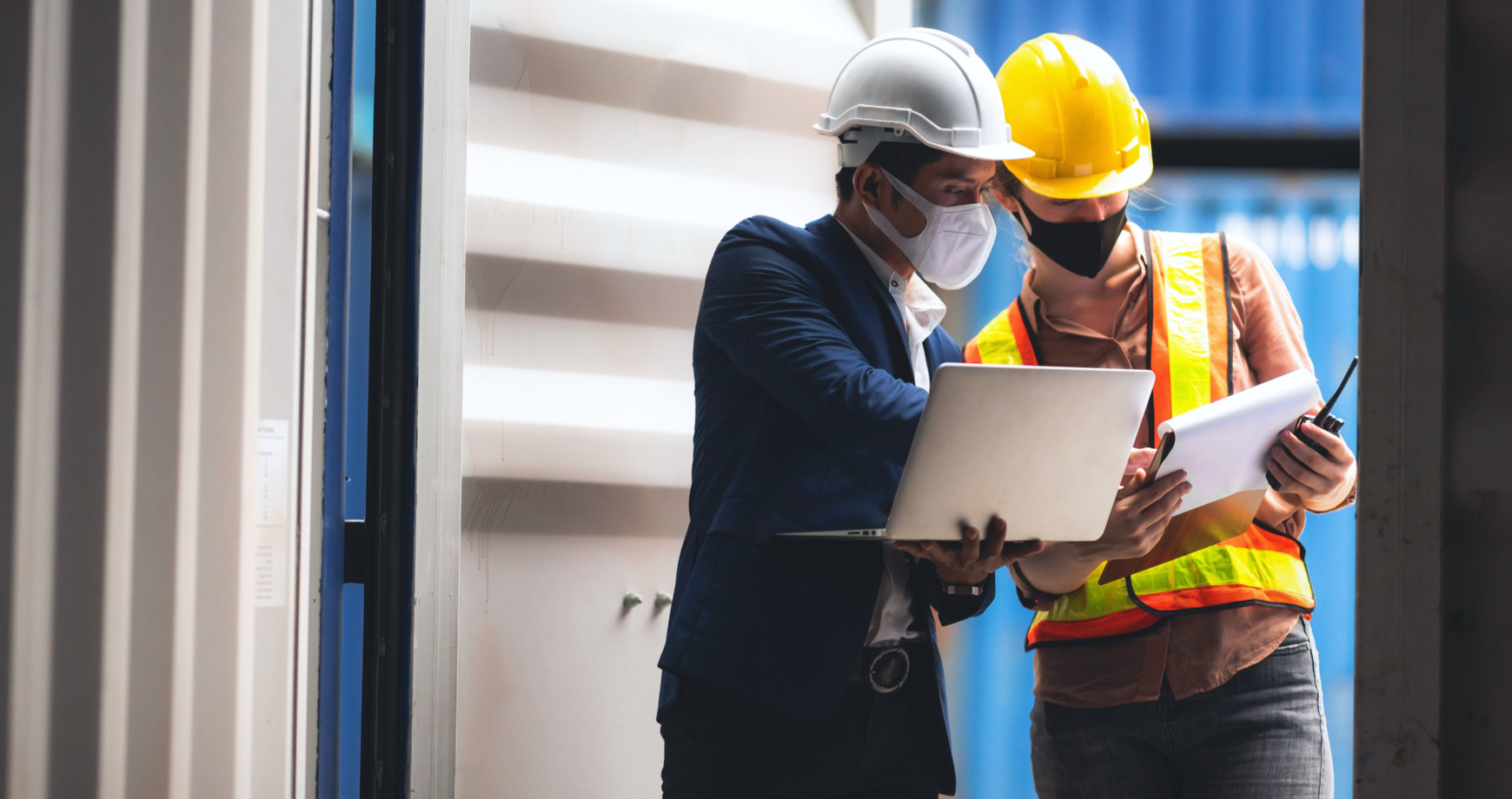
Salary
The Bureau of Labor Statistics does not monitor the salary of maintenance engineers, but job growth in related fields is projected. In general maintenance, engineers and mechanical technicians are expected to see eight percent growth, while construction management managers might see an 11 percent increase in their employment. You should therefore consider a career in maintenance engineering. Look for jobs in high-growth industries or entry-level roles within these industries.
Maintenance engineer salary in 2008: $88,570 was the median maintenance engineer salary. The lowest 25 percent earned $48,270, while the top ten percent earned more than $110,310.
FAQ
How does manufacturing avoid bottlenecks in production?
You can avoid bottlenecks in production by making sure that everything runs smoothly throughout the production cycle, from the moment you receive an order to the moment the product is shipped.
This includes both quality control and capacity planning.
Continuous improvement techniques like Six Sigma are the best way to achieve this.
Six Sigma Management System is a method to increase quality and reduce waste throughout your organization.
It focuses on eliminating variation and creating consistency in your work.
What is production plan?
Production Planning is the creation of a plan to cover all aspects, such as scheduling, budgeting. Location, crew, equipment, props and other details. It is important to have everything ready and planned before you start shooting. It should also contain information on achieving the best results on set. This includes information on shooting times, locations, cast lists and crew details.
The first step is to decide what you want. You might have an idea of where you want to film, or you may have specific locations or sets in mind. Once you have identified your locations and scenes it's time to begin figuring out what elements you will need for each one. Perhaps you have decided that you need to buy a car but aren't sure which model. This is where you can look up car models online and narrow down your options by choosing from different makes and models.
After you've found the perfect car, it's time to start thinking about adding extras. Do you need people sitting in the front seats? You might also need someone to help you get around the back. You may want to change the interior's color from black or white. These questions will help to determine the style and feel of your car. The type of shots that you are looking for is another thing to consider. Will you be filming close-ups or wide angles? Maybe you want the engine or the steering wheels to be shown. These things will help you to identify the car that you are looking for.
Once you have all the information, you are ready to create a plan. You can use a schedule to determine when and where you need it to be shot. A schedule for each day will detail when you should arrive at the location and when you need leave. Everyone will know what they need and when. Hire extra staff by booking them ahead of time. There is no point in hiring someone who won't turn up because you didn't let him know.
Your schedule will also have to be adjusted to reflect the number of days required to film. Some projects can be completed in a matter of days or weeks. Others may take several days. It is important to consider whether you require more than one photo per day when you create your schedule. Multiple takes at the same place will result in higher costs and longer completion times. If you are unsure if you need multiple takes, it is better to err on the side of caution and shoot fewer takes rather than risk wasting money.
Budget setting is an important part of production planning. It is important to set a realistic budget so you can work within your budget. If you have to reduce your budget due to unexpected circumstances, you can always lower it later. It is important to not overestimate how much you will spend. You will end up spending less money if you underestimate the cost of something.
Production planning is a complicated process. But once you understand how everything works together, it becomes much easier to plan future project.
What does it take to run a logistics business?
To run a successful logistics company, you need a lot knowledge and skills. To communicate effectively with clients and suppliers, you must be able to communicate well. You should be able analyse data and draw inferences. You must be able to work well under pressure and handle stressful situations. In order to innovate and create new ways to improve efficiency, creativity is essential. You will need strong leadership skills to motivate and direct your team members towards achieving their organizational goals.
You must be organized to meet tight deadlines.
What is manufacturing and logistics?
Manufacturing refers to the process of making goods using raw materials and machines. Logistics covers all aspects involved in managing supply chains, including procurement and production planning. Manufacturing and logistics can often be grouped together to describe a larger term that covers both the creation of products, and the delivery of them to customers.
What is the role of a production manager?
Production planners make sure that every aspect of the project is delivered on-time, within budget, and within schedule. They also ensure that the product/service meets the client’s needs.
What is the difference between a production planner and a project manager?
The main difference between a production planner and a project manager is that a project manager is usually the person who plans and organizes the entire project, whereas a production planner is mainly involved in the planning stage of the project.
Statistics
- (2:04) MTO is a production technique wherein products are customized according to customer specifications, and production only starts after an order is received. (oracle.com)
- In 2021, an estimated 12.1 million Americans work in the manufacturing sector.6 (investopedia.com)
- It's estimated that 10.8% of the U.S. GDP in 2020 was contributed to manufacturing. (investopedia.com)
- [54][55] These are the top 50 countries by the total value of manufacturing output in US dollars for its noted year according to World Bank.[56] (en.wikipedia.org)
- In the United States, for example, manufacturing makes up 15% of the economic output. (twi-global.com)
External Links
How To
How to Use 5S to Increase Productivity in Manufacturing
5S stands to stand for "Sort", “Set In Order", “Standardize", and "Store". The 5S methodology was developed at Toyota Motor Corporation in 1954. It helps companies achieve higher levels of efficiency by improving their work environment.
This method aims to standardize production processes so that they are repeatable, measurable and predictable. This means that every day tasks such cleaning, sorting/storing, packing, and labeling can be performed. This knowledge allows workers to be more efficient in their work because they are aware of what to expect.
Implementing 5S requires five steps. These are Sort, Set In Order, Standardize. Separate. And Store. Each step involves a different action which leads to increased efficiency. For example, when you sort things, you make them easy to find later. When you arrange items, you place them together. Next, organize your inventory into categories and store them in containers that are easily accessible. Labeling your containers will ensure that everything is correctly labeled.
This process requires employees to think critically about how they do their job. Employees must be able to see why they do what they do and find a way to achieve them without having to rely on their old methods. To be successful in the 5S system, employees will need to acquire new skills and techniques.
In addition to increasing efficiency, the 5S method also improves morale and teamwork among employees. They feel more motivated to work towards achieving greater efficiency as they see the results.