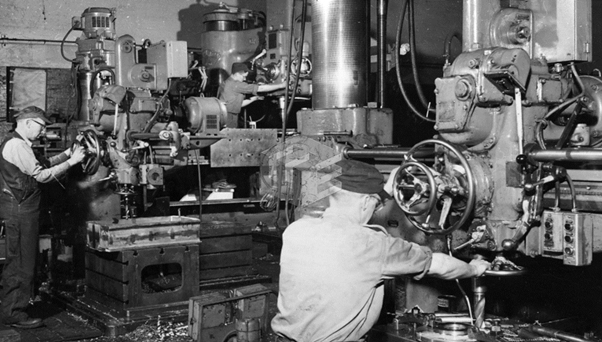
What is supply chain management? Supply chain management is a cross-functional process that manages relationships across the entire supply chain. Supply chain management helps improve business performance by improving operational and financial performance. This article will provide a basic definition of supply chain management and how it can improve your organization. Let's get started! What is supply chain management? Why is supply management so important? Here are a few examples of how it can benefit your business.
Supply chain management involves the management and coordination of all relationships in the supply chain
Products companies must consider how to acquire raw materials, create parts, and distribute finished products. The physical flow or goods is created by suppliers and then goes through different steps to reach a manufacturer, distributor and retailer before reaching the end consumer. Although some supply chains skip certain steps altogether, physical items need to be moved from one place to the next, stored for a while, and then be delivered to their destination. This process requires organization and planning.
Integration of all business functions is key to successful supply chain management. Vendors and suppliers need to have open communication. Information sharing helps both sides know what to expect and reduces costs. It also improves quality. Collaboration and communication within the supply chain can be improved through collaborative planning. Both parties will benefit. Customers should know about the company's operations and vendors must be able to deliver emergency supplies. Particularly important when selling perishable goods, lead times are critical.
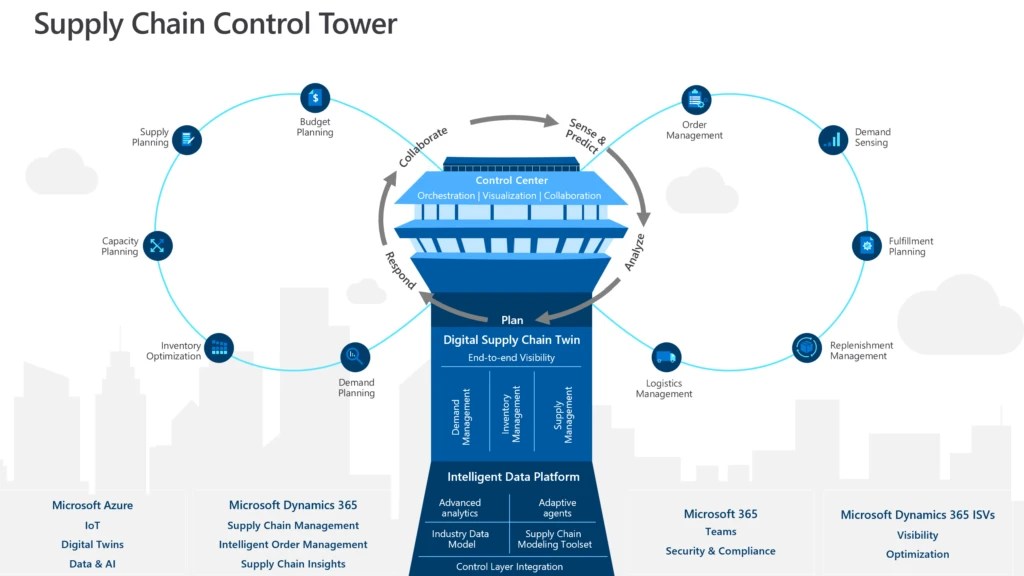
It is cross-functional and business-related.
There are many cross-functional factors that need to be considered when a company is looking at its supply chain. For a supply chain to be successful, suppliers need to be able delivery goods on time. That is why it is so important to coordinate. If companies follow the steps of Supply Chain Management, they can avoid many problems. This will improve efficiency and allow companies to save money.
Management needs to understand the interdependencies in the supply chain. They also need to work towards increasing profitability. Although all parties should reap the benefits of process improvements, it's important to set guidelines regarding how rewards are distributed. Some parties to the supply chain might not see the benefits of a better process unless they are based upon a common measurement system. If the value is not captured, it might be deemed ineffective.
It reduces operating cost
Streamlining your ordering process is one of the best ways to lower operating costs. Your employees will be less likely get lost or to order too many products if they use the same software program for all their requisitions. You can also reduce your operating expenses by setting up an approvals procedure to limit how many goods you order. A streamlined software system can help you avoid confusion and errors, monitor your inventory and order only what you need. It will also allow you to stop shipments being made if you are not required.
A second way to lower operating costs is to improve communication between warehouse workers. It is important to first analyze the current workflow, and then identify any bottlenecks or inefficiencies. When reducing transportation costs, look for ways to consolidate shipments or use dedicated transportation services. This will reduce your operating expenses by a substantial amount. You will be able to reduce your transportation costs and get your products to consumers faster.
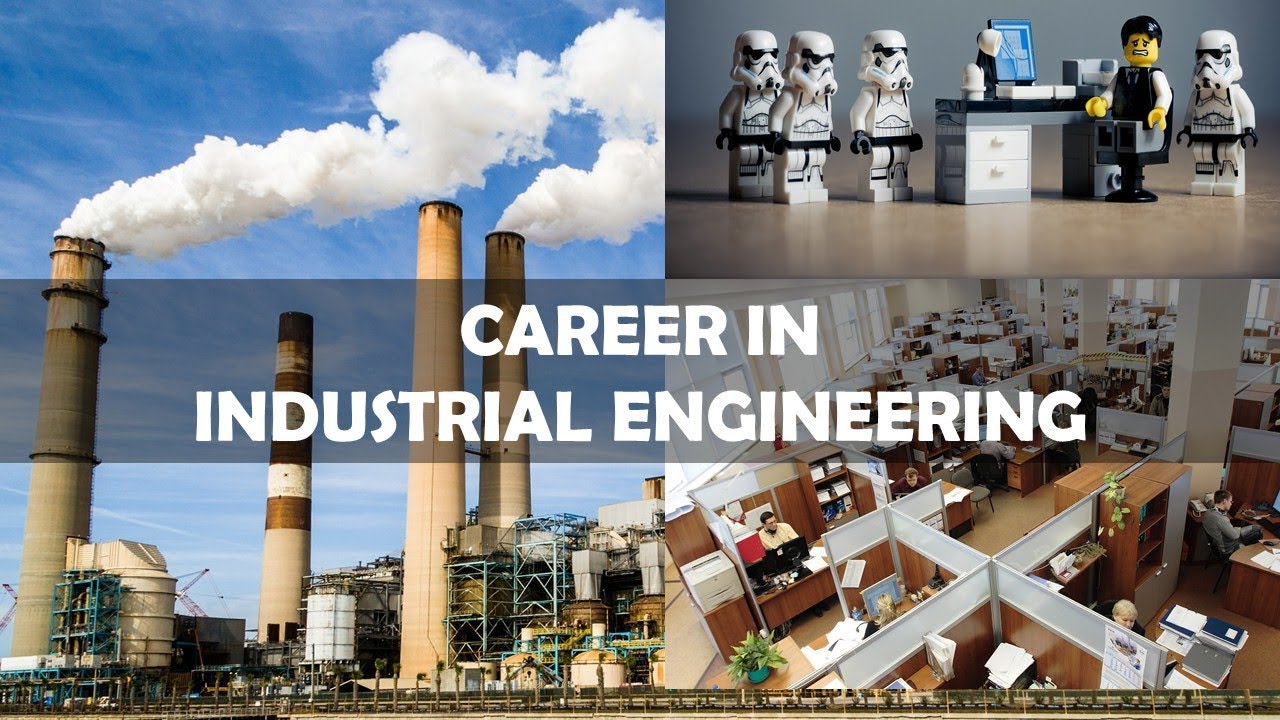
It improves your financial situation
A business's financial performance can be improved by supply chain management in many ways. Supply chain managers who are skilled in managing supply chains can help to reduce production costs and maximize variable costs. Profit margins can be increased by being able to control costs. Another benefit is the improvement of cash flow. The company can invoice customers more quickly if it delivers products faster to them. This reduces the need for expensive building space. A better supply chain also reduces the cost for fixed assets.
The Statement on Shareholders’ Equity (SSE), which summarizes ownership in a company, is a crucial financial statement. Improving a firm’s supply chain can boost after-tax liquidity by 8.5%. A company can decrease its costs by 10% while improving its supply chains performance. This will allow it to increase customer satisfaction and reduce its overall cost per unit. Supply chain management can improve financial performance and lead to greater operational efficiencies, which in turn leads to higher profits.
FAQ
What skills does a production planner need?
Production planners must be flexible, organized, and able handle multiple tasks. Effective communication with clients and colleagues is essential.
What are the requirements to start a logistics business?
It takes a lot of skills and knowledge to run a successful logistics business. To communicate effectively with clients and suppliers, you must be able to communicate well. You need to understand how to analyze data and draw conclusions from it. You must be able to work well under pressure and handle stressful situations. To improve efficiency, you must be innovative and creative. To motivate and guide your team towards reaching organizational goals, you must have strong leadership skills.
You must be organized to meet tight deadlines.
What are the products of logistics?
Logistics is the process of moving goods from one point to another.
They include all aspects associated with transport including packaging, loading transporting, unloading storage, warehousing inventory management customer service, distribution returns and recycling.
Logisticians ensure the product reaches its destination in the most efficient manner. They assist companies with their supply chain efficiency through information on demand forecasts. Stock levels, production times, and availability.
They can also track shipments in transit and monitor quality standards.
Statistics
- Job #1 is delivering the ordered product according to specifications: color, size, brand, and quantity. (netsuite.com)
- You can multiply the result by 100 to get the total percent of monthly overhead. (investopedia.com)
- In the United States, for example, manufacturing makes up 15% of the economic output. (twi-global.com)
- Many factories witnessed a 30% increase in output due to the shift to electric motors. (en.wikipedia.org)
- (2:04) MTO is a production technique wherein products are customized according to customer specifications, and production only starts after an order is received. (oracle.com)
External Links
How To
How to Use 5S for Increasing Productivity in Manufacturing
5S stands in for "Sort", the "Set In Order", "Standardize", or "Separate". Toyota Motor Corporation was the first to develop the 5S approach in 1954. It allows companies to improve their work environment, thereby achieving greater efficiency.
This method aims to standardize production processes so that they are repeatable, measurable and predictable. This means that every day tasks such cleaning, sorting/storing, packing, and labeling can be performed. Because workers know what they can expect, this helps them perform their jobs more efficiently.
There are five steps that you need to follow in order to implement 5S. Each step is a different action that leads to greater efficiency. For example, when you sort things, you make them easy to find later. When you set items in an order, you put items together. Then, after you separate your inventory into groups, you store those groups in containers that are easy to access. Make sure everything is correctly labeled when you label your containers.
Employees must be able to critically examine their work practices. Employees must understand why they do certain tasks and decide if there's another way to accomplish them without relying on the old ways of doing things. To implement the 5S system, employees must acquire new skills and techniques.
The 5S method not only increases efficiency but also boosts morale and teamwork. As they begin to see improvements, they feel motivated to continue working towards the goal of achieving higher levels of efficiency.