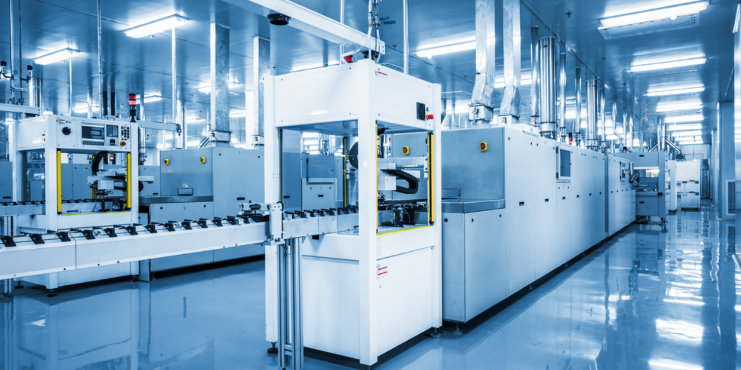
The duties of a mechanical engineer technician vary depending on the employer. They might test equipment, review blueprints, make purchase requests and do research to improve mechanical processes. They may also be exposed at times to potentially hazardous substances. These risks are minimized with the use of proper procedures.
While a mechanical engineer may supervise a technician who is a mechanical engineer, the technician's duties are typically performed independently. They are responsible to maintain and repair machinery and equipment. They are responsible for ensuring safety and compliance with company policies. Customers' requirements must also be met.
A competent mechanical engineering technician will solve mechanical problems and do accurate calculations. They may also work closely alongside engineers to improve production processes. They might also assist in the design and testing of new materials.
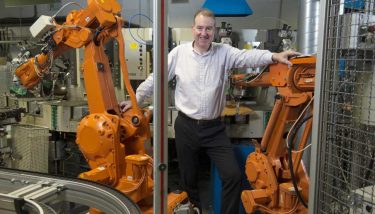
A mechanical engineering technician should have a good understanding of principles and practices in mechanical engineering to be able to do the best job. They will need to be proficient in using CAD software, which allows them to design and analyze machines. They must also be able maintain service records. Aside from that, they must be able demonstrate exceptional time management skills.
Mechanical engineers technicians are most commonly responsible for testing equipment and making estimations. Additionally, they might conduct research to improve manufacturing process. These findings are typically recorded and evaluated making them an important part a technician in mechanical engineering.
Another job of a mechanical engineer technician is to prepare drawings for components, interpret instructions, write work orders and interpret instructions. Mechanical engineers may also test electrical systems, equipment, and materials to see how they work. They can also help design industrial machinery and power generation plants. They may also be able to perform statistical studies in order to evaluate the production's costs.
To become a successful mechanic technician you must have a solid understanding of mechanical engineering principles, critical thinking skills and an eye for detail. Additionally, you may need to be able to use new technology. As a part of the engineering team, you will need to create sketches and other graphic representations of mechanical systems. You also have to test them under different operational conditions.
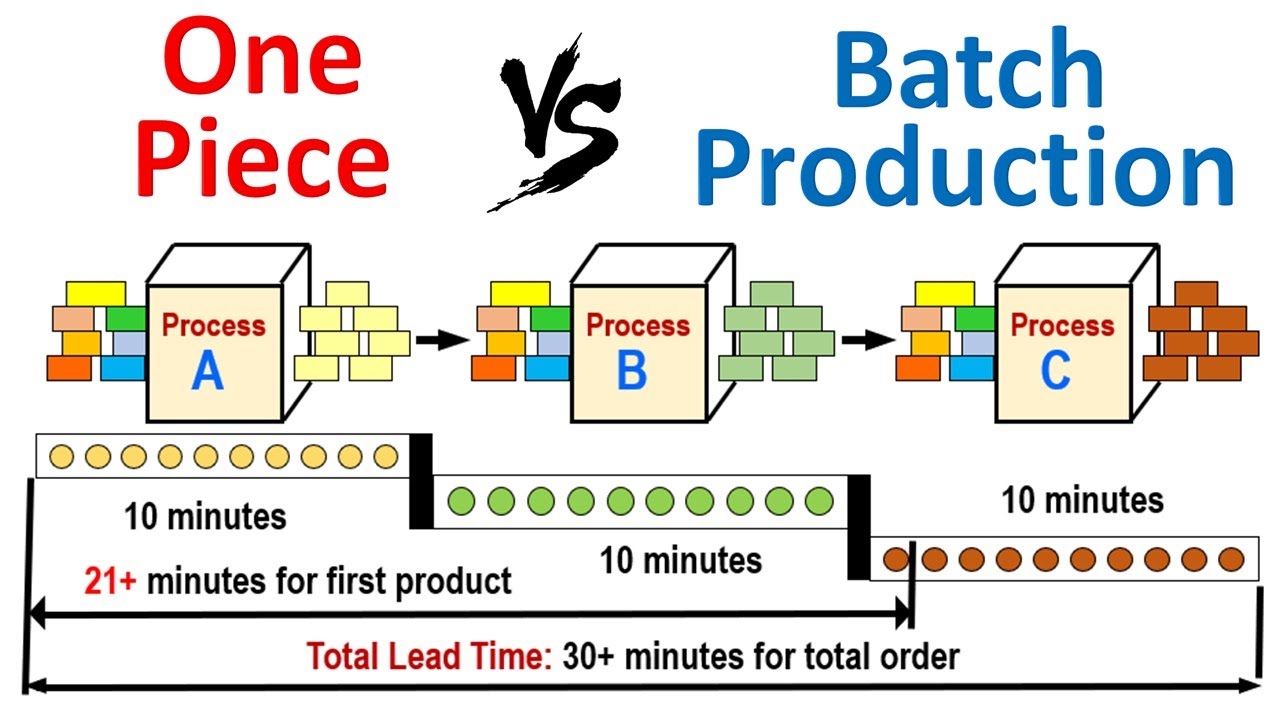
Quality control analysis is another important part of the job of a mechanical engineer technician. Engineers perform quality control analysis by comparing tool drawings to the original specifications. They may also make improvements and record the results. The results may be submitted to engineering departments.
A mechanical engineer technician will work a lot alone but they will still be able to work regularly. They might also work overtime if necessary. They might work in a laboratory, research facility, or manufacturing factory. They could be required to work long hours and are exposed to potentially harmful materials.
A mechanical engineer technician may also need to deal with hydraulics, and other power sources. They will be required to use power tools and rigging equipment every day and meet the demands of their customers.
FAQ
What is meant by manufacturing industries?
Manufacturing Industries refers to businesses that manufacture products. Consumers are those who purchase these products. This is accomplished by using a variety of processes, including production, distribution and retailing. They make goods from raw materials with machines and other equipment. This includes all types if manufactured goods.
Why is logistics important in manufacturing?
Logistics are an essential part of any business. They help you achieve great results by helping you manage all aspects of product flow, from raw materials to finished goods.
Logistics also play a major role in reducing costs and increasing efficiency.
What are the 7 R's of logistics?
The acronym "7R's" of Logistics stands for seven principles that underpin logistics management. It was developed by International Association of Business Logisticians (IABL), and published as part of their "Seven Principles of Logistics Management Series" in 2004.
The acronym consists of the following letters:
-
Responsible - to ensure that all actions are within the legal requirements and are not detrimental to others.
-
Reliable - Have confidence in your ability to fulfill all of your commitments.
-
Use resources effectively and sparingly.
-
Realistic - Consider all aspects of operations, including environmental impact and cost effectiveness.
-
Respectful - treat people fairly and equitably.
-
Reliable - Find ways to save money and increase your productivity.
-
Recognizable - provide customers with value-added services.
What are the four types in manufacturing?
Manufacturing refers to the transformation of raw materials into useful products by using machines and processes. It includes many different activities like designing, building and testing, packaging, shipping and selling, as well as servicing.
How can manufacturing efficiency improved?
The first step is to determine the key factors that impact production time. We then need to figure out how to improve these variables. If you aren't sure where to begin, think about the factors that have the greatest impact on production time. Once you've identified them, try to find solutions for each of those factors.
What are the responsibilities of a production planner
A production planner ensures all aspects of the project are delivered on time, within budget, and within scope. A production planner ensures that the service and product meet the client's expectations.
Statistics
- According to a Statista study, U.S. businesses spent $1.63 trillion on logistics in 2019, moving goods from origin to end user through various supply chain network segments. (netsuite.com)
- [54][55] These are the top 50 countries by the total value of manufacturing output in US dollars for its noted year according to World Bank.[56] (en.wikipedia.org)
- Job #1 is delivering the ordered product according to specifications: color, size, brand, and quantity. (netsuite.com)
- In the United States, for example, manufacturing makes up 15% of the economic output. (twi-global.com)
- According to the United Nations Industrial Development Organization (UNIDO), China is the top manufacturer worldwide by 2019 output, producing 28.7% of the total global manufacturing output, followed by the United States, Japan, Germany, and India.[52][53] (en.wikipedia.org)
External Links
How To
How to Use Just-In-Time Production
Just-in time (JIT), is a process that reduces costs and increases efficiency in business operations. It's a way to ensure that you get the right resources at just the right time. This means that only what you use is charged to your account. The term was first coined by Frederick Taylor, who developed his theory while working as a foreman in the early 1900s. He saw how overtime was paid to workers for work that was delayed. He concluded that if workers were given enough time before they start work, productivity would increase.
The idea behind JIT is that you should plan ahead and have everything ready so you don't waste money. You should also look at the entire project from start to finish and make sure that you have sufficient resources available to deal with any problems that arise during the course of your project. If you anticipate that there might be problems, you'll have enough people and equipment to fix them. This way, you won't end up paying extra money for things that weren't really necessary.
There are several types of JIT techniques:
-
Demand-driven JIT: This is a JIT that allows you to regularly order the parts/materials necessary for your project. This will allow for you to track the material that you have left after using it. It will also allow you to predict how long it takes to produce more.
-
Inventory-based: You stock materials in advance to make your projects easier. This allows you to predict how much you can expect to sell.
-
Project-driven: This method allows you to set aside enough funds for your project. Knowing how much money you have available will help you purchase the correct amount of materials.
-
Resource-based JIT: This is the most popular form of JIT. This is where you assign resources based upon demand. If you have many orders, you will assign more people to manage them. If you don't have many orders, you'll assign fewer people to handle the workload.
-
Cost-based: This approach is very similar to resource-based. However, you don't just care about the number of people you have; you also need to consider how much each person will cost.
-
Price-based: This approach is very similar to the cost-based method except that you don't look at individual workers costs but the total cost of the company.
-
Material-based is an alternative to cost-based. Instead of looking at the total cost in the company, this method focuses on the average amount of raw materials that you consume.
-
Time-based JIT: A variation on resource-based JIT. Instead of focusing on how much each employee costs, you focus on how long it takes to complete the project.
-
Quality-based JIT: This is another variation of resource based JIT. Instead of thinking about how much each employee costs or how long it takes to manufacture something, you think about how good the quality of your product is.
-
Value-based JIT: One of the most recent forms of JIT. In this case, you're not concerned with how well the products perform or whether they meet customer expectations. Instead, you are focused on adding value to the marketplace.
-
Stock-based: This stock-based method focuses on the actual quantity of products being made at any given time. It's useful when you want maximum production and minimal inventory.
-
Just-intime (JIT), planning is a combination JIT management and supply chain management. It is the process of scheduling components' delivery as soon as they have been ordered. It reduces lead times and improves throughput.